Method for controlling consistency of vibration of surfaces of shell structures on basis of neural networks
A technology of surface vibration and shell structure, applied in the direction of adaptive control, general control system, control/regulation system, etc., can solve the problems of increasing equipment quality, high replacement cost, limited low frequency vibration suppression effect, etc., to improve stability The effect of resistance and anti-interference
- Summary
- Abstract
- Description
- Claims
- Application Information
AI Technical Summary
Problems solved by technology
Method used
Image
Examples
Embodiment Construction
[0035] Below in conjunction with accompanying drawing and specific embodiment the content of the present invention is described in further detail:
[0036] A method for controlling surface vibration consistency of a shell structure of the present invention comprises the following steps:
[0037] (1) Construct the overall structure of vibration consistency control to guide the overall operation of the control system.
[0038] figure 1 Shown is a schematic diagram of the shell controlled by vibration consistency. The core link includes two parts: the controller NNC and the identifier NNI. Among them, the identifier is responsible for the identification and response prediction of the controlled shell, and the controller is responsible for optimizing the excitation parameters and realizing the control target. In addition, "sampling" refers to the process of data acquisition and collection; "T→F" refers to the conversion process of time domain to frequency domain data; [D] refers...
PUM
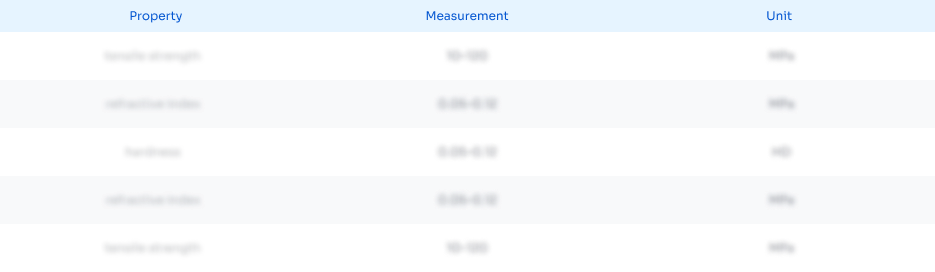
Abstract
Description
Claims
Application Information

- R&D
- Intellectual Property
- Life Sciences
- Materials
- Tech Scout
- Unparalleled Data Quality
- Higher Quality Content
- 60% Fewer Hallucinations
Browse by: Latest US Patents, China's latest patents, Technical Efficacy Thesaurus, Application Domain, Technology Topic, Popular Technical Reports.
© 2025 PatSnap. All rights reserved.Legal|Privacy policy|Modern Slavery Act Transparency Statement|Sitemap|About US| Contact US: help@patsnap.com