Preparation method of rust-proof treatment fluid for inner wall of gearbox
A technology of anti-rust treatment and preparation method, applied in the field of surface treatment, can solve the problems of rough surface, difficult treatment, rust, etc., and achieve the effects of low cost, long anti-rust period and good corrosion resistance
- Summary
- Abstract
- Description
- Claims
- Application Information
AI Technical Summary
Problems solved by technology
Method used
Examples
Embodiment 1
[0017] A method for preparing an anti-rust treatment liquid for the inner wall of a gearbox, the composition of the anti-rust treatment liquid is calculated by weight percentage: 8% oxalic acid, 9% triethanolamine, 5% citric acid, 8% sodium petroleum sulfonate, fatty alcohol Polyoxyethylene ether 5.5%, ammonium molybdate 5%, sodium benzoate 2%, sodium hydroxide 2.5%, technical ethanol 2%, ethylene glycol 3.5%, surplus is water; Described preparation method is:
[0018] 1) Add industrial ethanol and ethylene glycol into the container, then add triethanolamine and fatty alcohol polyoxyethylene ether, stir to dissolve evenly;
[0019] 2) Add an appropriate amount of water to another container, then add oxalic acid, citric acid, sodium petroleum sulfonate, ammonium sulfonate, sodium benzoate and sodium hydroxide in sequence, and stir for 3 minutes for each substance added, when the sodium hydroxide is added After stirring for 15 minutes, then add the solution prepared in step 1), ...
Embodiment 2
[0021] A method for preparing an anti-rust treatment liquid for the inner wall of a gearbox, the composition of the anti-rust treatment liquid is calculated by weight percentage: 10% oxalic acid, 7% triethanolamine, 7% citric acid, 6% sodium petroleum sulfonate, fatty alcohol Polyoxyethylene ether 6.5%, ammonium molybdate 3%, sodium benzoate 4%, sodium hydroxide 1.5%, technical ethanol 4%, ethylene glycol 1.5%, surplus is water; Described preparation method is:
[0022] 1) Add industrial ethanol and ethylene glycol into the container, then add triethanolamine and fatty alcohol polyoxyethylene ether, stir to dissolve evenly;
[0023] 2) Add an appropriate amount of water to another container, then add oxalic acid, citric acid, sodium petroleum sulfonate, ammonium sulfonate, sodium benzoate and sodium hydroxide in sequence, and stir for 5 minutes for each substance added, when the sodium hydroxide is added After stirring for 10 minutes, then add the solution prepared in step 1),...
Embodiment 3
[0025] A method for preparing an anti-rust treatment liquid for the inner wall of a gearbox. The composition of the anti-rust treatment liquid is calculated by weight percentage: 9% oxalic acid, 8% triethanolamine, 6% citric acid, 7% sodium petroleum sulfonate, fatty alcohol Polyoxyethylene ether 6.0%, ammonium molybdate 4%, sodium benzoate 3%, sodium hydroxide 2.0%, technical ethanol 3%, ethylene glycol 2.5%, surplus is water; Described preparation method is:
[0026] 1) Add industrial ethanol and ethylene glycol into the container, then add triethanolamine and fatty alcohol polyoxyethylene ether, stir to dissolve evenly;
[0027] 2) Add an appropriate amount of water to another container, then add oxalic acid, citric acid, sodium petroleum sulfonate, ammonium sulfonate, sodium benzoate and sodium hydroxide in sequence, and stir for 4 minutes for each substance added, when the sodium hydroxide is added After stirring for 13 minutes, then add the solution prepared in step 1), ...
PUM
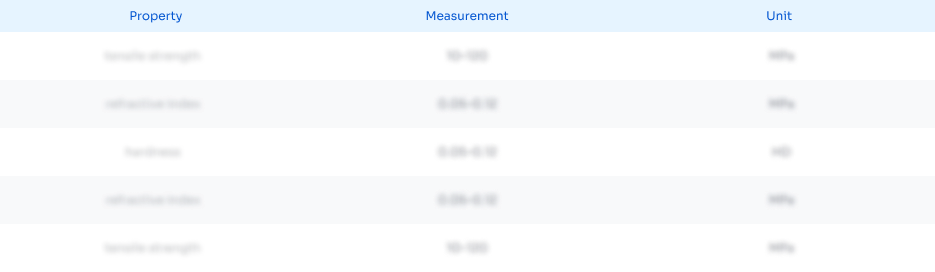
Abstract
Description
Claims
Application Information

- R&D Engineer
- R&D Manager
- IP Professional
- Industry Leading Data Capabilities
- Powerful AI technology
- Patent DNA Extraction
Browse by: Latest US Patents, China's latest patents, Technical Efficacy Thesaurus, Application Domain, Technology Topic, Popular Technical Reports.
© 2024 PatSnap. All rights reserved.Legal|Privacy policy|Modern Slavery Act Transparency Statement|Sitemap|About US| Contact US: help@patsnap.com