Realize the processing technology and fixture structure of multi-material substrates with simultaneous printing and patching
A technology of substrates and fixtures, applied in printing, printing machines, rotary printing machines, etc., can solve the problems of difficult matching of the number of substrates, low production efficiency, waste of production materials, etc., and achieve balance of processing volume, cost saving, and production reduction cost effect
- Summary
- Abstract
- Description
- Claims
- Application Information
AI Technical Summary
Problems solved by technology
Method used
Image
Examples
Embodiment 1
[0040] Embodiment one: see Figure 1~3 As shown, a jig structure that realizes the simultaneous printing and patching process of multiple material substrates, including bearing jigs, vacuum jigs and printing screens, wherein:
[0041] The carrying jig includes a body 10, which is provided with several kinds of substrate positioning grooves 16, the number of each substrate positioning groove 16 matches the ratio of the number of substrates corresponding to the product demand, and the bottom of the substrate positioning groove 16 open with through holes;
[0042] The vacuum jig is used in conjunction with the carrying jig, and it includes a support column 12 corresponding to each of the substrate positioning grooves 16, and each support column 12 is provided with several vacuum holes 13;
[0043] The printing screen is used in conjunction with the carrying jig, and corresponding to each of the substrate positioning grooves 16, there are several mesh holes 15 corresponding to th...
Embodiment 2
[0059] Embodiment two: see Figure 4 As shown, a multi-material substrate simultaneously prints a patch process and its jig structure. In this embodiment, its jig structure and process are similar to those of Embodiment 1. The difference lies in: the PCB substrate 30 required for the product One, one DBC substrate 31, the number of the two required is 2:1, so there are 10+5 substrate positioning grooves 32 on the carrying fixture, the upper two rows are 5+5 PCB substrate positioning grooves, and the lower row There are five DBC substrate positioning grooves. Similarly, the positions of the support columns on the vacuum jig and the mesh holes on the printing screen are matched with the substrate positioning grooves on the carrying jig to achieve simultaneous printing.
PUM
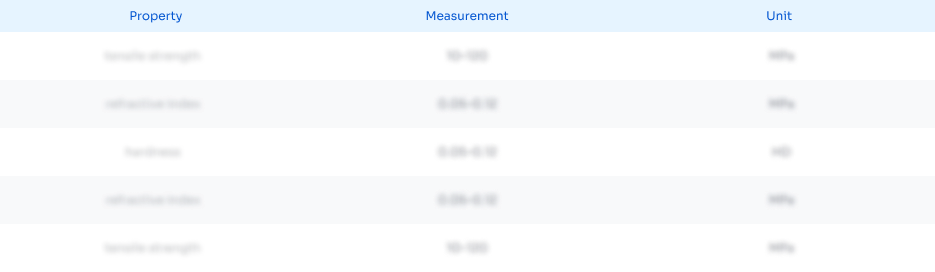
Abstract
Description
Claims
Application Information

- R&D
- Intellectual Property
- Life Sciences
- Materials
- Tech Scout
- Unparalleled Data Quality
- Higher Quality Content
- 60% Fewer Hallucinations
Browse by: Latest US Patents, China's latest patents, Technical Efficacy Thesaurus, Application Domain, Technology Topic, Popular Technical Reports.
© 2025 PatSnap. All rights reserved.Legal|Privacy policy|Modern Slavery Act Transparency Statement|Sitemap|About US| Contact US: help@patsnap.com