Calcium carbide powder forming equipment and process for machining calcium carbide powder into calcium carbide balls or blocks
A molding equipment, calcium carbide powder technology, applied in material molding presses, manufacturing tools, presses, etc., can solve the problems of excessive calcium carbide powder dust, low efficiency, difficult work for workers, etc. The effect of rolling damage
- Summary
- Abstract
- Description
- Claims
- Application Information
AI Technical Summary
Problems solved by technology
Method used
Image
Examples
example 1
[0042] Calcium carbide powder, calcium carbonate, talcum powder, polyethylene acetate emulsion and borax are proportioned by weight percentage: calcium carbide powder: 100; calcium carbonate: 10; talcum powder: 5; polyethylene acetate emulsion: 2; borax: 1.
[0043] The generation time of calcium carbide powder in this embodiment is 12h-36h, and the static pressure provided by the hydraulic system is 150-300 tons;
[0044] generation time Hydrostatic pressure Gas output L / kg Compression KN Drop strength 12 150 121.75 40 Not broken, powder-free 24 220 115.67 41 not broken 36 300 108.11 39 not broken 12 220 122.56 45 Not broken, powder-free 24 300 115.99 44 not broken 36 150 98.06 36 broken into small pieces 12 300 124.89 52 Not broken, powder-free 24 150 112.91 40 not broken 36 220 122.87 38 Finely crushed
example 2
[0046] Calcium carbide powder, calcium carbonate, talcum powder, polyethylene acetate emulsion and borax are proportioned by weight percentage: calcium carbide powder: 100; calcium carbonate: 15; talcum powder: 15; polyethylene acetate emulsion: 3; borax: 1.5.
[0047] In this embodiment, the generation time of calcium carbide powder is 12h-36h, and the static pressure provided by the hydraulic system is 150-300 tons;
[0048] generation time Hydrostatic pressure Gas output L / kg Compression KN Drop strength 12 150 122.15 41 Not broken, powder-free 24 220 116.17 42 not broken 36 300 108.91 40 not broken 12 220 123.53 45.5 Not broken, powder-free 24 300 116.11 45 not broken 36 150 98.96 37 broken into small pieces 12 300 124.90 53 Not broken, powder-free 24 150 113.12 42 not broken 36 220 122.17 39 Finely crushed
example 3
[0050] Calcium carbide powder, talcum powder, polyethylene acetate emulsion and borax are proportioned by weight percentage: calcium carbide powder: 100; calcium carbonate: 30; talcum powder: 15; polyethylene acetate emulsion: 5; borax: 2.
[0051] In this embodiment, the generation time of calcium carbide powder is 12h-36h, and the static pressure provided by the hydraulic system is 150-300 tons;
[0052] generation time Hydrostatic pressure Gas output L / kg Compression KN Drop strength 12 150 122.98 42 Not broken, powder-free 24 220 116.76 43 not broken 36 300 109.00 41 not broken 12 220 123.87 46 Not broken, powder-free 24 300 116.66 46 not broken 36 150 99.01 38 broken into small pieces 12 300 125.00 54 Not broken, powder-free 24 150 113.89 43 not broken 36 220 122.77 41 Finely crushed
[0053] The above data shows that through high pressure (usually above 200), the compac...
PUM
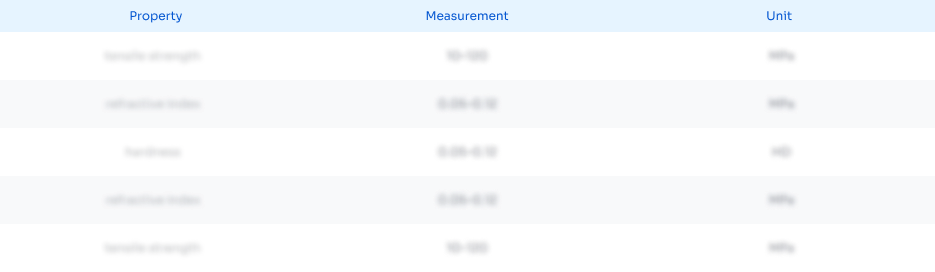
Abstract
Description
Claims
Application Information

- R&D
- Intellectual Property
- Life Sciences
- Materials
- Tech Scout
- Unparalleled Data Quality
- Higher Quality Content
- 60% Fewer Hallucinations
Browse by: Latest US Patents, China's latest patents, Technical Efficacy Thesaurus, Application Domain, Technology Topic, Popular Technical Reports.
© 2025 PatSnap. All rights reserved.Legal|Privacy policy|Modern Slavery Act Transparency Statement|Sitemap|About US| Contact US: help@patsnap.com