Back-blowing flue gas filtering system and operating method thereof
A filtration system and working method technology, applied in separation methods, dispersed particle filtration, chemical instruments and methods, etc., can solve problems such as backflush flue gas containing dust, reduce the difficulty of cleaning dust, and increase the gap between filter bags and cages, etc. To achieve the effect of improving technical advantages, improving market competitiveness, and avoiding dust accumulation in filter bags
- Summary
- Abstract
- Description
- Claims
- Application Information
AI Technical Summary
Problems solved by technology
Method used
Image
Examples
Embodiment Construction
[0020] The specific implementation plan is as follows:
[0021] A backflush flue gas filtering system, comprising one or more backflush pipelines (1) drawn from a backflush gas source, each backflush pipeline is provided with a three-way (2), and a valve one (3), Valve two (7), valve one (3) are connected to back blowing section one (6), and back blowing section one is connected in series with back blowing flue gas filter device (4), back blowing booster fan (5), back blowing section One end is connected to the dust removal system (9) of the blowback bag filter; the second valve (7) is connected to the second blowback section (8), and the second blowback section (8) is directly connected to the dust removal system of the blowback bag filter (9) connected, back blowing section one (6) and back blowing section two (8) are in parallel relationship, this back blowing flue gas filtration system is used in the back blowing bag filter When the filter bag is damaged and the dust cont...
PUM
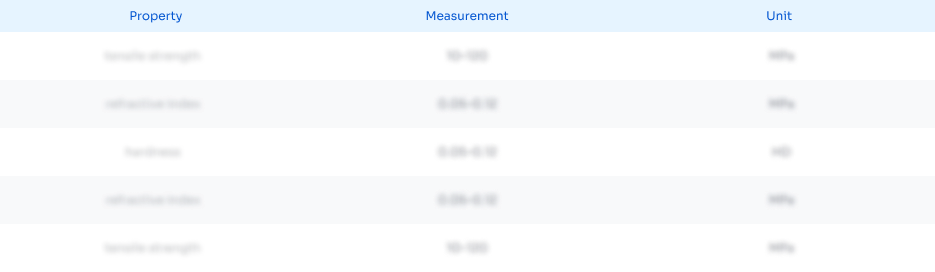
Abstract
Description
Claims
Application Information

- Generate Ideas
- Intellectual Property
- Life Sciences
- Materials
- Tech Scout
- Unparalleled Data Quality
- Higher Quality Content
- 60% Fewer Hallucinations
Browse by: Latest US Patents, China's latest patents, Technical Efficacy Thesaurus, Application Domain, Technology Topic, Popular Technical Reports.
© 2025 PatSnap. All rights reserved.Legal|Privacy policy|Modern Slavery Act Transparency Statement|Sitemap|About US| Contact US: help@patsnap.com