Multi-step vacuum filtration plate base
A technology of vacuum suction filtration and filter plate, applied in gravity filter and other directions, can solve problems such as single function, and achieve the effect of improving single function, enhanced function and convenient operation.
- Summary
- Abstract
- Description
- Claims
- Application Information
AI Technical Summary
Problems solved by technology
Method used
Image
Examples
Embodiment Construction
[0008] figure 1 Shown is a vacuum suction filter plate seat with three stepped surfaces, which includes a seat body 1, the upper end of which is an open end, and the lower end is connected with a suction hole 4.
[0009] In the center of the seat body 1, three sets of filter plate seats 2 arranged up and down are provided. The diameter of the filter plate seat close to the upper end of the seat body 1 is larger than the diameter of the filter plate seat away from the upper end of the seat body. The seat on the outer periphery of each filter plate seat 2 Annular sealing grooves 3 are respectively arranged on the body, and the lower end of the filter plate seat 2 at the lowermost end communicates with the air extraction hole 4 .
[0010] The design of the filter plate seat is not limited to the above example, see the claims for the specific design scope, and its use is based on the actual needs of production, and the filter plate seat is flexibly selected.
PUM
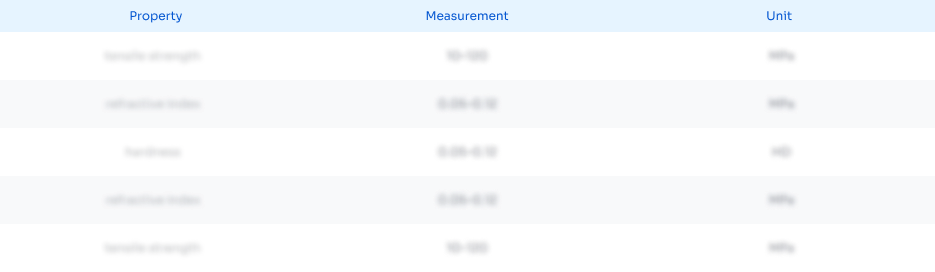
Abstract
Description
Claims
Application Information

- Generate Ideas
- Intellectual Property
- Life Sciences
- Materials
- Tech Scout
- Unparalleled Data Quality
- Higher Quality Content
- 60% Fewer Hallucinations
Browse by: Latest US Patents, China's latest patents, Technical Efficacy Thesaurus, Application Domain, Technology Topic, Popular Technical Reports.
© 2025 PatSnap. All rights reserved.Legal|Privacy policy|Modern Slavery Act Transparency Statement|Sitemap|About US| Contact US: help@patsnap.com