Device and method for double-shaft shoulder FSW (Friction Stir Welding) based on temperature feedback of leader region
A friction stir welding and temperature feedback technology, applied in welding equipment, non-electric welding equipment, metal processing equipment, etc., can solve the problems of metal overheating in the welding area, coarse grains in the welding area, affecting the welding quality, etc., to achieve high detection accuracy, The effect of high welding quality and high degree of welding automation
- Summary
- Abstract
- Description
- Claims
- Application Information
AI Technical Summary
Problems solved by technology
Method used
Image
Examples
Embodiment Construction
[0031] The present invention will be further described below in conjunction with the accompanying drawings.
[0032] Such as Figure 1 to Figure 7 As shown, a dual-shaft shoulder friction stir welding device based on the temperature feedback of the leading zone of the present invention includes a stirring head 1, a holder 3 installed on the head of the friction stir welding machine, and moves synchronously with the head of the friction stir welding machine The trolley, the stirring head 1 is clamped on the machine head by the clamper 3, and a semicircular arc magnetic steel sheet 5 is fixed on the machine head, and a high-speed proximity switch is installed at every 90° in the circumferential direction of the clamper 3, The stirring head 1 comprises an upper shoulder 1-1, a lower shoulder 1-2 and a stirring needle 1-3 between the upper shoulder 1-1 and the lower shoulder 1-2, and in the circumferential direction of the upper shoulder 1-1 An armored thermocouple 2 is installed a...
PUM
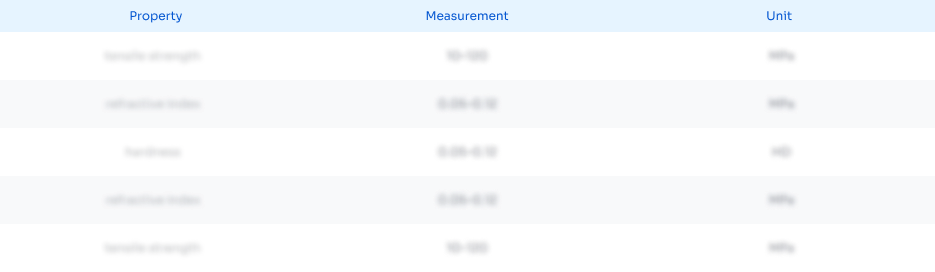
Abstract
Description
Claims
Application Information

- R&D
- Intellectual Property
- Life Sciences
- Materials
- Tech Scout
- Unparalleled Data Quality
- Higher Quality Content
- 60% Fewer Hallucinations
Browse by: Latest US Patents, China's latest patents, Technical Efficacy Thesaurus, Application Domain, Technology Topic, Popular Technical Reports.
© 2025 PatSnap. All rights reserved.Legal|Privacy policy|Modern Slavery Act Transparency Statement|Sitemap|About US| Contact US: help@patsnap.com