A modification method of in-situ crystallization type catalytic cracking catalyst
A catalytic cracking and in-situ crystallization technology, applied in physical/chemical process catalysts, molecular sieve catalysts, chemical instruments and methods, etc. The effect of improving catalyst performance, reducing ammonia nitrogen pollution and low sodium oxide content
- Summary
- Abstract
- Description
- Claims
- Application Information
AI Technical Summary
Problems solved by technology
Method used
Image
Examples
Embodiment 1
[0052] Put 500g of crystallization product 1, sodium hydroxide and deionized water into a stainless steel kettle under stirring, sodium hydroxide / crystallization product = 0.15, exchange at 95°C for 1 hour, remove the filtrate by filtration, and deionize the filter cake with deionized water Wash until the pH value is less than 10 to obtain the alkali-treated product; the alkali-treated product, ammonium sulfate and deionized water, ammonium sulfate / alkali-treated product=0.05, exchange at pH=3.0~3.5, 90°C for 1.5 hours, and filter to remove the filtrate , the filter cake was washed with deionized water and dried to obtain an exchange material; the first exchange material was exchanged with rare earth chloride once more, and the exchange conditions were: rare earth / an exchange material=0.05, pH=3.5-4.2, and the temperature was 90°C. The time is 1 hour, and the exchanged material is filtered, washed, and dried to obtain the second batch; the second batch is roasted at 550 ° C and...
Embodiment 2
[0054] Put 500g of crystallization product 2, potassium hydroxide and deionized water into a stainless steel kettle under stirring, potassium hydroxide / crystallization product=0.08, exchange at 85°C for 1 hour, remove the filtrate by filtration, and use deionized water for the filter cake Wash until the pH value is less than 10 to obtain the alkali-treated product; the alkali-treated product, ammonium sulfate and deionized water, ammonium chloride / alkali-treated product=0.09, exchange at pH=3.0~3.5, 90°C for 2 hours, and filter to remove The filtrate and the filter cake were washed with deionized water and dried to obtain an exchange material; the first exchange material was exchanged with rare earth nitrate once again, and the exchange conditions were: rare earth / one exchange material=0.045, pH=3.5-4.2, and the temperature was 90°C. The time is 1 hour, and the exchanged material is filtered, washed, and dried to obtain the second batch; the second batch is roasted at 600°C and...
Embodiment 3
[0056] Put 500g of crystallization product 3, sodium hydroxide and deionized water into a stainless steel kettle under stirring, sodium hydroxide / crystallization product=0.01, exchange at 75°C for 3 hours, filter to remove the filtrate, and deionize the filter cake with deionized water Wash until the pH value is less than 10 to obtain the alkali-treated product; the alkali-treated product, ammonium nitrate and deionized water, ammonium nitrate / alkali-treated product=0.15, exchange at pH=3.0-3.5, 90°C for 2 hours, and filter to remove the filtrate , the filter cake was washed with deionized water and dried to obtain an exchange material; the first exchange material was exchanged with rare earth nitrate once again, the exchange conditions were: rare earth / an exchange material=0.06, pH=3.5~4.2, temperature was 90°C, time For 1 hour, the exchanged material was filtered, washed, and dried to obtain the second batch; the second batch was roasted at 620°C and the water vapor intake wa...
PUM
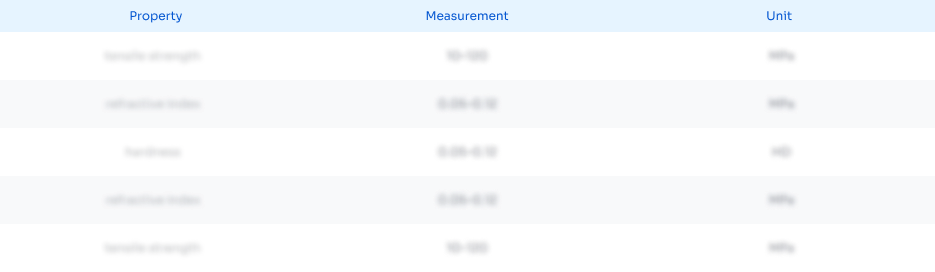
Abstract
Description
Claims
Application Information

- R&D
- Intellectual Property
- Life Sciences
- Materials
- Tech Scout
- Unparalleled Data Quality
- Higher Quality Content
- 60% Fewer Hallucinations
Browse by: Latest US Patents, China's latest patents, Technical Efficacy Thesaurus, Application Domain, Technology Topic, Popular Technical Reports.
© 2025 PatSnap. All rights reserved.Legal|Privacy policy|Modern Slavery Act Transparency Statement|Sitemap|About US| Contact US: help@patsnap.com