Preparation method of organic silicon defoamer
A technology of silicone defoamer and production method, which is applied in the direction of defoamer, etc., and can solve problems such as ineffective effect and large amount of defoamer
- Summary
- Abstract
- Description
- Claims
- Application Information
AI Technical Summary
Problems solved by technology
Method used
Examples
Embodiment 1
[0008] The invention provides a method for preparing an organosilicon defoamer, comprising the following raw materials in parts by weight: 30 parts of simethicone oil, 28 parts of silicone grease, 15 parts of polyoxyethylene stearate, trihard sorbitan 12 parts of fatty acid ester, 120 parts of water; also include the following steps: heating 1 / 3 of the above 120 parts of water to 60°C, adding sorbitan tristearate and polyoxyethylene stearate under stirring , after melting evenly, add silicone grease and simethicone under stirring, add the remaining water while maintaining 60°C, and continue stirring for 40 minutes to obtain a defoamer.
[0009] The invention provides a method for making an organosilicon defoamer. The prepared defoamer is suitable for papermaking and other industries such as automobile antifreeze. Adding 20g of defoamer to 1 ton of pulp can achieve good results .
Embodiment 2
[0011] The invention provides a method for making an organosilicon defoamer, which comprises the following raw materials in parts by weight: 40 parts of simethicone oil, 38 parts of silicone grease, 18 parts of polyoxyethylene stearate, trihard sorbitan 18 parts of fatty acid ester, 143 parts of water; also include the following steps: heating 1 / 3 of the above 143 parts of water to 68°C, adding sorbitan tristearate and polyoxyethylene stearate under stirring After melting evenly, add silicone grease and simethicone oil under stirring, add the remaining water while maintaining 68°C, and continue stirring for 40 minutes to obtain a defoamer.
[0012] The invention provides a method for making an organosilicon defoamer. The prepared defoamer is suitable for papermaking and other industries such as automobile antifreeze. Adding 20g of defoamer to 1 ton of pulp can achieve good results .
Embodiment 3
[0014] The invention provides a method for making an organosilicon defoamer, which comprises the following raw materials in parts by weight: 35 parts of dimethyl silicone oil, 30 parts of silicone grease, 16 parts of polyoxyethylene stearate, trihard sorbitan 16 parts of fatty acid ester, 135 parts of water; also include the following steps: heating 1 / 3 of the above 135 parts of water to 65°C, adding sorbitan tristearate and polyoxyethylene stearate under stirring , after melting evenly, add silicone grease and simethicone under stirring, add the remaining water while maintaining 65°C, and continue stirring for 40 minutes to prepare a defoamer.
[0015] The invention provides a method for making an organosilicon defoamer. The prepared defoamer is suitable for papermaking and other industries such as automobile antifreeze. Adding 20g of defoamer to 1 ton of pulp can achieve good results . .
PUM
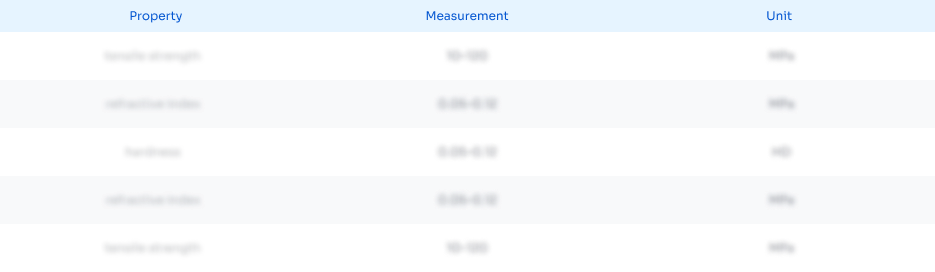
Abstract
Description
Claims
Application Information

- R&D Engineer
- R&D Manager
- IP Professional
- Industry Leading Data Capabilities
- Powerful AI technology
- Patent DNA Extraction
Browse by: Latest US Patents, China's latest patents, Technical Efficacy Thesaurus, Application Domain, Technology Topic, Popular Technical Reports.
© 2024 PatSnap. All rights reserved.Legal|Privacy policy|Modern Slavery Act Transparency Statement|Sitemap|About US| Contact US: help@patsnap.com