Non-coaxial disc-type magnetic gear
A magnetic gear and disc technology, applied in electrical components, electromechanical devices, etc., can solve the problems of low torque density and low utilization rate of permanent magnets, and achieve a simplified structure, improved energy transfer efficiency, and reduced noise and vibration. Effect
- Summary
- Abstract
- Description
- Claims
- Application Information
AI Technical Summary
Problems solved by technology
Method used
Image
Examples
Embodiment 1
[0017] Embodiment 1: as figure 1 As shown, the disc-type magnetic gear with different axes includes an inner rotor, an outer rotor and a magnetic adjustment structure; both the inner rotor and the outer rotor adopt a disc structure and are placed along different axes, and the inner rotor is placed inside the outer rotor and connected to the outer rotor. The height of the rotor is equal.
[0018] Both the inner rotor and the outer rotor include N-pole permanent magnets and S-pole permanent magnets, and the pole arc coefficients are both 0.6. Wherein, the permanent magnets of the inner rotor have three pairs of poles, and the permanent magnets of the outer rotor have ten pairs of poles. The inner rotor is composed of an N-pole permanent magnet 2 , an S-pole permanent magnet 3 and an inner rotor yoke 1 magnetized in the axial direction. Wherein, the N-pole permanent magnets 2 and S-pole permanent magnets 3 of the inner rotor are interlaced and attached to the surface of the inn...
Embodiment 2
[0021] Embodiment 2: In this embodiment, the difference from Embodiment 1 is only that the N-pole permanent magnet 2 and the S-pole permanent magnet 3 of the inner rotor are embedded in the inner rotor yoke 1; the N-pole permanent magnet 4 of the outer rotor and S pole permanent magnets 5 are embedded in the outer rotor yoke 6 .
PUM
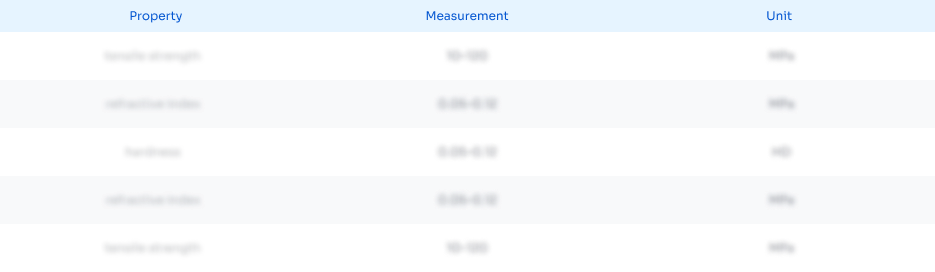
Abstract
Description
Claims
Application Information

- Generate Ideas
- Intellectual Property
- Life Sciences
- Materials
- Tech Scout
- Unparalleled Data Quality
- Higher Quality Content
- 60% Fewer Hallucinations
Browse by: Latest US Patents, China's latest patents, Technical Efficacy Thesaurus, Application Domain, Technology Topic, Popular Technical Reports.
© 2025 PatSnap. All rights reserved.Legal|Privacy policy|Modern Slavery Act Transparency Statement|Sitemap|About US| Contact US: help@patsnap.com