A mineral processing method for processing low-grade tin-lead-zinc polymetallic oxide ore
A technology of polymetallic oxidation ore and mineral processing methods, applied in chemical instruments and methods, flotation, wet separation, etc., can solve the problem of failing to fully consider the rational link and overall optimization of the entire process of mineral processing and smelting, and failing to achieve low-grade oxidation Efficient development and utilization of lead-zinc mines, lead-zinc recovery rate less than 40%, etc., to achieve the effect of simplifying tin recovery process, easy control, and improving lead-zinc recovery rate
- Summary
- Abstract
- Description
- Claims
- Application Information
AI Technical Summary
Problems solved by technology
Method used
Image
Examples
Embodiment 1
[0030] A beneficiation method for processing low-grade tin-lead-zinc polymetallic oxide ore. The raw ore composition of low-grade tin-lead-zinc polymetallic oxide ore: 0.27% tin, 0.88% lead, 0.52% antimony, 76.6g / t silver, zinc 1.06%, indium 38.5g / t, lead oxidation rate 92.45%, zinc oxidation rate 91.30%.
[0031] Above-mentioned raw ore is passed through following processing steps:
[0032] (1) Grinding: After the raw ore is crushed, the ore is ground to -200 mesh, about 70%.
[0033] (2) Grading shaker beneficiation: Divide the grinding product into -0.2mm~+0.074mm, -0.074mm two grain grades, send the raw ore with -0.2mm~+0.074mm grain grade to a section of fine sand shaker for heavy For the beneficiation operation, the ore concentration is about 25%; the raw ore with a particle size of -0.074mm is sent to a section of grooved shaker for gravity separation, and the ore concentration is about 20%; the mixed coarse concentrate of tin, lead, antimony, silver, zinc and indium, ...
Embodiment 2
[0042] A beneficiation method for processing low-grade tin-lead-zinc polymetallic oxide ore, the raw ore composition of low-grade tin-lead-zinc polymetallic oxide ore: 0.54% tin, 1.43% lead, 0.82% antimony, 80.4g / t silver, zinc 4.12%, indium 41.2g / t, lead oxidation rate 93.12%, zinc oxidation rate 92.15%.
[0043] Above-mentioned raw ore is passed through following processing steps:
[0044] (1) Grinding: After the raw ore is crushed, the ore is ground to -200 mesh, about 75%.
[0045] (2) Grading shaker beneficiation: Divide the grinding product into -0.2mm~+0.074mm, -0.074mm two grain grades, send the raw ore with -0.2mm~+0.074mm grain grade to a section of fine sand shaker for heavy For the beneficiation operation, the ore concentration is about 20%; the raw ore with a particle size of -0.074mm is sent to a section of grooved shaker for gravity separation, and the ore concentration is about 15%; the mixed coarse concentrate of tin, lead, antimony, silver, zinc and indium, ...
Embodiment 3
[0054] A beneficiation method for processing low-grade tin-lead-zinc polymetallic oxide ore. The raw ore composition of low-grade tin-lead-zinc polymetallic oxide ore: 0.71% tin, 2.81% lead, 1.87% antimony, 95.6g / t silver, zinc 1.52%, indium 52.2g / t, lead oxidation rate 93.12%, zinc oxidation rate 92.15%.
[0055] Above-mentioned raw ore is passed through following processing steps:
[0056] (1) Grinding: After the raw ore is crushed, the ore is ground to -200 mesh, about 70%.
[0057] (2) Grading shaker beneficiation: Divide the grinding product into -0.2mm~+0.074mm, -0.074mm two grain grades, send the raw ore with -0.2mm~+0.074mm grain grade to a section of fine sand shaker for heavy For the beneficiation operation, the ore concentration is about 20%; the raw ore with a particle size of -0.074mm is sent to a section of grooved shaker for gravity separation, and the ore concentration is about 15%; the mixed coarse concentrate of tin, lead, antimony, silver, zinc and indium, ...
PUM
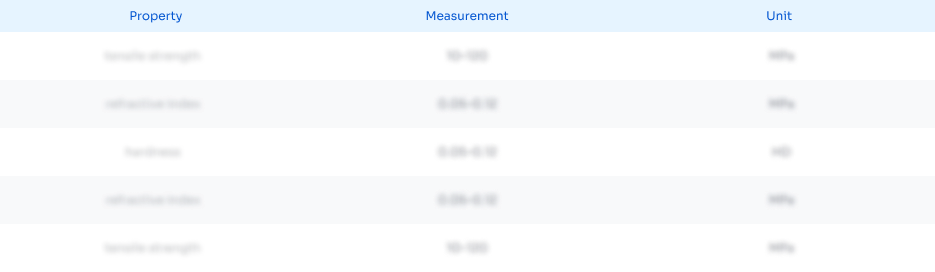
Abstract
Description
Claims
Application Information

- R&D Engineer
- R&D Manager
- IP Professional
- Industry Leading Data Capabilities
- Powerful AI technology
- Patent DNA Extraction
Browse by: Latest US Patents, China's latest patents, Technical Efficacy Thesaurus, Application Domain, Technology Topic, Popular Technical Reports.
© 2024 PatSnap. All rights reserved.Legal|Privacy policy|Modern Slavery Act Transparency Statement|Sitemap|About US| Contact US: help@patsnap.com