Assembly method of ball joint coupling and ball joint base of ball joint coupling
A ball joint seat and coupling technology, applied in the direction of coupling, elastic coupling, engine lubrication, etc., can solve the problem of cumbersome assembly of ball joint coupling, achieve simple and convenient assembly process, and improve lubrication effect. , the effect of reducing production costs
- Summary
- Abstract
- Description
- Claims
- Application Information
AI Technical Summary
Problems solved by technology
Method used
Image
Examples
Embodiment Construction
[0018] Embodiment 1 of the spherical hinge seat of the spherical hinge coupling in the present invention is as Figure 1-2 Shown: the ball hinge seat of the ball joint coupling, including the sleeve body 1 and the flange 2 integrally connected to the outer peripheral surface of the sleeve body 1, the inner peripheral surface of the sleeve body 1 is a spherical surface for the ball and the positioning ball The matching inner concave spherical surface 11 is provided with two key grooves 112 extending radially along the sleeve body 1 and used for mating with the head of the force transmission block on the inner concave spherical surface 11. The two key grooves 112 are symmetrically distributed on the sleeve body At both ends of the radial direction of 1, the sleeve body 1 is an integral structure, and the concave spherical surface 11 is provided with an installation groove 113 for inserting the positioning ball along the axial direction of the sleeve body. The installation groove ...
PUM
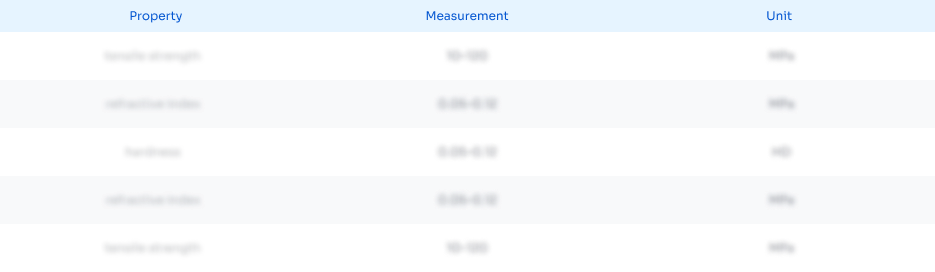
Abstract
Description
Claims
Application Information

- R&D
- Intellectual Property
- Life Sciences
- Materials
- Tech Scout
- Unparalleled Data Quality
- Higher Quality Content
- 60% Fewer Hallucinations
Browse by: Latest US Patents, China's latest patents, Technical Efficacy Thesaurus, Application Domain, Technology Topic, Popular Technical Reports.
© 2025 PatSnap. All rights reserved.Legal|Privacy policy|Modern Slavery Act Transparency Statement|Sitemap|About US| Contact US: help@patsnap.com