Fault diagnosis system and method for fuel delivery pump
An oil pump, piezoelectric technology, applied in the field of oil pump fault diagnosis system, can solve the problems of poor flexibility, difficult replacement, low functional accuracy, etc., to achieve the effect of improving efficiency and accuracy
- Summary
- Abstract
- Description
- Claims
- Application Information
AI Technical Summary
Problems solved by technology
Method used
Image
Examples
Embodiment 1
[0021] see figure 1 , a specific fuel pump diagnosis system includes: a first piezoelectric acceleration sensor, a second piezoelectric acceleration sensor, a third piezoelectric acceleration sensor, a fourth piezoelectric acceleration sensor, a first temperature sensor, a second temperature sensor sensor, a third temperature sensor, a fourth temperature sensor, a fifth temperature sensor, a temperature measurement module, a signal conditioner, a data acquisition card and an industrial control computer;
[0022] The first piezoelectric acceleration sensor, the second piezoelectric acceleration sensor, the third piezoelectric acceleration sensor, and the fourth piezoelectric acceleration sensor are respectively connected to the signal conditioner;
[0023] The signal conditioner, the data acquisition card and the industrial control computer are connected in sequence;
[0024] The first temperature sensor, the second temperature sensor, the third temperature sensor, the fourth ...
Embodiment 2
[0029] A method for diagnosing an oil pump failure, comprising the steps of:
[0030] 1) The vibration signal acquisition step is to obtain the vibration signal and temperature signal generated by the oil transfer pump through four piezoelectric acceleration sensors and five temperature sensors;
[0031] 2) a signal conditioning step, conditioning and outputting the signal input by the piezoelectric acceleration sensor through a signal conditioner;
[0032] 3) The data collection step is used to collect the signal output by the signal conditioner and the signal uploaded by the temperature measurement module, and upload the collected signal to the industrial control computer;
[0033] 4) The signal analysis step is used to calculate and analyze the vibration signal and temperature signal generated by the oil delivery pump, and diagnose the failure of the oil delivery pump.
[0034] Further, in the step 4), the specific analysis method is to analyze the vibration signal in time...
PUM
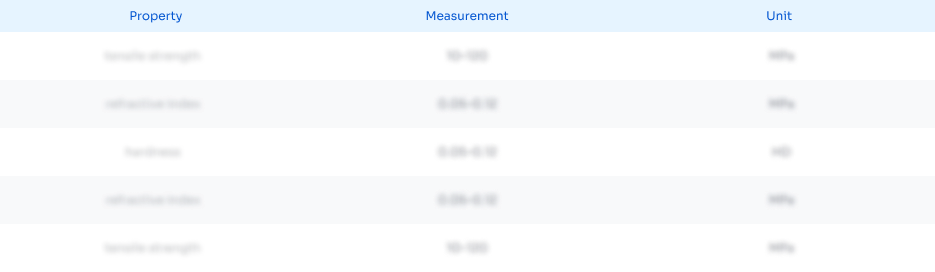
Abstract
Description
Claims
Application Information

- R&D Engineer
- R&D Manager
- IP Professional
- Industry Leading Data Capabilities
- Powerful AI technology
- Patent DNA Extraction
Browse by: Latest US Patents, China's latest patents, Technical Efficacy Thesaurus, Application Domain, Technology Topic, Popular Technical Reports.
© 2024 PatSnap. All rights reserved.Legal|Privacy policy|Modern Slavery Act Transparency Statement|Sitemap|About US| Contact US: help@patsnap.com