Pressure head device of sand jetting mechanism of upper pressing type core making machine
A core making machine and indenter technology, applied in molding machines, manufacturing tools, casting and molding equipment, etc., can solve the problems of loosening and falling off at the fixed part of the hose, large thermal energy loss of catalytic gas, and sand shooting energy loss, etc., to reduce thermal energy. The effect of reducing the loss of sand shot energy and saving the cost of spare parts
- Summary
- Abstract
- Description
- Claims
- Application Information
AI Technical Summary
Problems solved by technology
Method used
Image
Examples
Embodiment 1
[0041] see Figure 1-Figure 3 , as shown in the legend, a pressure head device of the sand shooting mechanism of the upper pressure core making machine, including:
[0042] A frame is provided with a support plate 11 installed horizontally;
[0043] A lifting guide mechanism, including a guide sleeve 21 assembled on the support plate 11 with the axis perpendicular to the support plate 11, and a guide rod 22 slidingly penetrated in the guide sleeve 21;
[0044] A hydraulic cylinder 3 is installed on the upper side of the support plate 11 and its drive is connected to the upper end of the guide rod 22;
[0045] A pressure head 4 is arranged below the support plate 11 and driven to connect to the lower end of the guide rod 22. The pressure head 4 is also provided with a ventilation flow channel 51, and the ventilation flow channel 51 has a first flow channel port 511 and a second flow channel port. 512, the first flow channel port 511 is located on the pressing surface of the p...
Embodiment 2
[0067] The rest is the same as the first embodiment, except that the upper port of the first ventilation guide sleeve is set as the above-mentioned first ventilation port.
Embodiment 3
[0069] The rest is the same as the first or second embodiment, except that the above-mentioned sand shooting air bag is set on an independent air bag support.
PUM
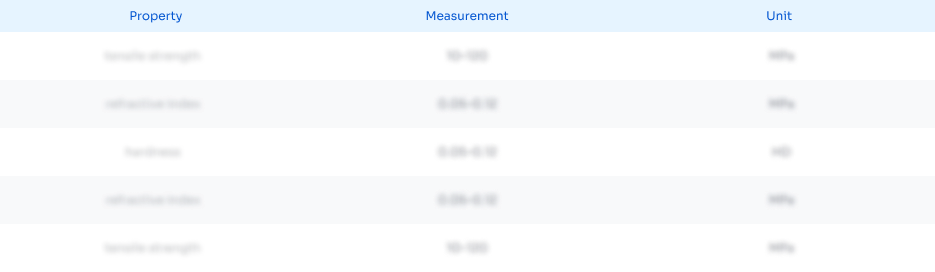
Abstract
Description
Claims
Application Information

- Generate Ideas
- Intellectual Property
- Life Sciences
- Materials
- Tech Scout
- Unparalleled Data Quality
- Higher Quality Content
- 60% Fewer Hallucinations
Browse by: Latest US Patents, China's latest patents, Technical Efficacy Thesaurus, Application Domain, Technology Topic, Popular Technical Reports.
© 2025 PatSnap. All rights reserved.Legal|Privacy policy|Modern Slavery Act Transparency Statement|Sitemap|About US| Contact US: help@patsnap.com