Servo-type acceleration sensor
An acceleration sensor, servo-type technology, applied in the direction of measurement of acceleration, speed/acceleration/shock measurement, instruments, etc., can solve the problems of increased assembly man-hours, non-oriented miniaturization, and large current flow
- Summary
- Abstract
- Description
- Claims
- Application Information
AI Technical Summary
Problems solved by technology
Method used
Image
Examples
Embodiment Construction
[0039] The implementation of the present invention will be described below with reference to the accompanying drawings. The servo type acceleration sensor 1 of embodiment, as figure 1 As shown, it includes a sensor unit 2 , a servo circuit unit 3 , a housing 4 and a base member 5 . The sensor unit 2 is attached to the base member 5 , and the servo circuit unit 3 is attached to the sensor unit 2 .
[0040] Such as figure 2 As shown, the sensor part 2 includes a vibrator part 6, a frame part 7, a first housing 8, a second housing 9, two spacers 10a, 10b, and the like. The shape of the sensor unit 2 is substantially cylindrical, with a height of about 15 mm and an outer diameter of about 23 mm.
[0041] The vibrator part 6 and the frame part 7 sandwich and bond the thin metal plate member 11 via a pair of vibrator part printed circuit boards 12a, 12b and frame part printed circuit boards 17a, 17b, respectively. Coils 13 a , 13 b are mounted on vibrator portion printed circui...
PUM
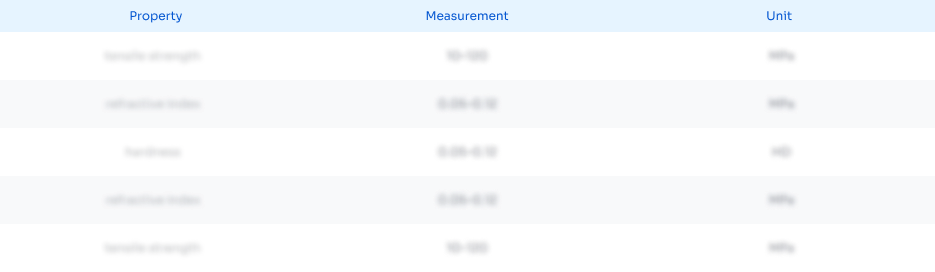
Abstract
Description
Claims
Application Information

- R&D
- Intellectual Property
- Life Sciences
- Materials
- Tech Scout
- Unparalleled Data Quality
- Higher Quality Content
- 60% Fewer Hallucinations
Browse by: Latest US Patents, China's latest patents, Technical Efficacy Thesaurus, Application Domain, Technology Topic, Popular Technical Reports.
© 2025 PatSnap. All rights reserved.Legal|Privacy policy|Modern Slavery Act Transparency Statement|Sitemap|About US| Contact US: help@patsnap.com