Preparation method of fiber-base-fabric foamed epoxy resin cloth
A technology of epoxy resin and fiber cloth, which is applied in the processing of textile materials, textile and papermaking, liquid/gas/vapor textile processing, etc. Small batch production, simple equipment and process, easy to adjust the effect of the formula
- Summary
- Abstract
- Description
- Claims
- Application Information
AI Technical Summary
Problems solved by technology
Method used
Examples
Embodiment Construction
[0011] The basic principle of the present invention is: Utilize the physical strength of (weaving) fiber base cloth to resist pulling, impregnate the fiber cloth into solvent-type foaming epoxy resin, make the fiber base cloth and foaming epoxy resin combine, greatly expand the development The scope and accuracy of foaming epoxy resin.
[0012] The object to be achieved by the present invention is to provide a novel preparation method for producing fiber cloth-based foamed epoxy resin cloth for the defects of the prior art. This method has the characteristics of simple process, less investment, convenient formula adjustment and small batch production; it is especially suitable for the production of thick fiber cloth.
[0013] A method for preparing a fiber cloth-based foamed epoxy resin cloth according to the present invention belongs to a solvent-based preparation method. The raw materials used in the method include a fiber cloth base, a foaming agent, an epoxy resin and a so...
PUM
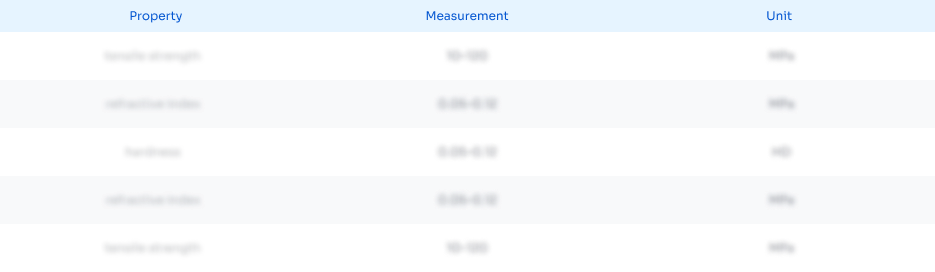
Abstract
Description
Claims
Application Information

- R&D
- Intellectual Property
- Life Sciences
- Materials
- Tech Scout
- Unparalleled Data Quality
- Higher Quality Content
- 60% Fewer Hallucinations
Browse by: Latest US Patents, China's latest patents, Technical Efficacy Thesaurus, Application Domain, Technology Topic, Popular Technical Reports.
© 2025 PatSnap. All rights reserved.Legal|Privacy policy|Modern Slavery Act Transparency Statement|Sitemap|About US| Contact US: help@patsnap.com