High-pressure blower
A high-pressure blower and air barrel technology, which is applied in mechanical equipment, machines/engines, liquid fuel engines, etc., can solve problems such as motor damage, achieve the effects of prolonging service life, good toughness, and improving mechanical properties
- Summary
- Abstract
- Description
- Claims
- Application Information
AI Technical Summary
Problems solved by technology
Method used
Image
Examples
Embodiment 1
[0042] Weigh the raw materials according to the composition elements and mass percentages of the bearing cover plate and the bearing described in Example 1 in Table 1, and the composition elements and mass percentages of the bearing cover plate and the bearing have a certain influence on the performance of the bearing cover plate and the bearing. , and its preparation process also has a great influence on the performance of the final bearing cover plate and bearing. The preparation method of the bearing cover plate and the bearing includes a forging process and heat treatment; in the forging process, the initial forging temperature is 1110°C, and the final forging temperature is 810°C; in the heat treatment process, quenching is performed when the temperature is 860°C, After that, keep warm for 3 hours; temper when the temperature is 480°C, and then keep warm for 3 hours after tempering.
Embodiment 2
[0044] Weigh raw materials according to the composition elements and mass percentages of the bearing cover plate and bearing described in Table 1 Example 2, the composition elements and mass percentages of the bearing cover plate and bearing have certain influence on the performance of the bearing cover plate and bearing , and its preparation process also has a great influence on the performance of the final bearing cover plate and bearing. The preparation method of the bearing cover plate and the bearing includes a forging process and heat treatment; in the forging process, the initial forging temperature is 1100°C, and the final forging temperature is 780°C; in the heat treatment process, quenching is performed when the temperature is 850°C, After that, keep warm for 2 hours; temper when the temperature is 470°C, and then keep warm for 3 hours after tempering.
Embodiment 3
[0046] Weigh the raw materials according to the composition elements and mass percentages of bearing cover plate and bearing described in Table 1 Example 3, and the composition elements and mass percentages of bearing cover plate and bearing have certain influence on the performance of bearing cover plate and bearing , and its preparation process also has a great influence on the performance of the final bearing cover plate and bearing. The preparation method of the bearing cover plate and the bearing includes a forging process and heat treatment; in the forging process, the initial forging temperature is 1140°C, and the final forging temperature is 830°C; in the heat treatment process, quenching is performed when the temperature is 950°C, After that, keep warm for 4 hours; temper when the temperature is 520°C, and then keep warm for 4 hours after tempering.
PUM
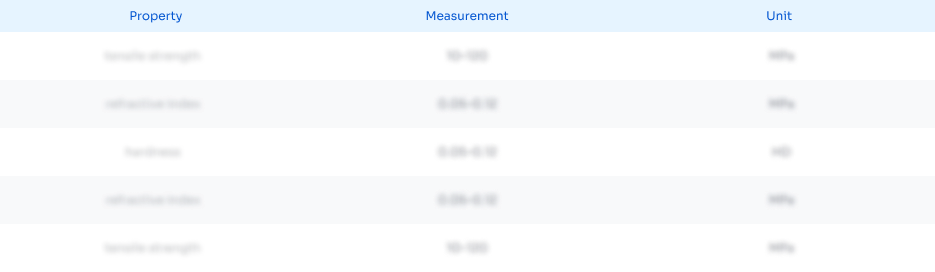
Abstract
Description
Claims
Application Information

- R&D
- Intellectual Property
- Life Sciences
- Materials
- Tech Scout
- Unparalleled Data Quality
- Higher Quality Content
- 60% Fewer Hallucinations
Browse by: Latest US Patents, China's latest patents, Technical Efficacy Thesaurus, Application Domain, Technology Topic, Popular Technical Reports.
© 2025 PatSnap. All rights reserved.Legal|Privacy policy|Modern Slavery Act Transparency Statement|Sitemap|About US| Contact US: help@patsnap.com