Inorganic-filling material full-biodegradation composite material with high compatibility and preparation method thereof
A technology of inorganic filler and composite material, which is applied in the field of fully biodegradable composite material and its preparation, can solve the problems of poor compatibility between master batch carrier and polyester matrix, and achieves good processing performance, reduced preparation cost and good compatibility. Effect
- Summary
- Abstract
- Description
- Claims
- Application Information
AI Technical Summary
Benefits of technology
Problems solved by technology
Method used
Image
Examples
Embodiment 1
[0042] (1) Dry PLA (4032D, NatureWorks) in a blast oven at 60°C for 24h, and calcium carbonate (1250 mesh) in a blast oven at 105°C for 10h.
[0043] (2) Take 90 parts of calcium carbonate, add it to the high mixer, stir at low speed, spray 0.5 parts of silane coupling agent KH550 while stirring, then stir at high speed for 5 minutes, then add 10 parts of PLA and 0.5 parts of compatibilizer ADR -4368 (manufactured by BASF), 0.6 part of calcium stearate, 0.1 part of antioxidant tetrakis [β-(3,5-di-tert-butyl-4-hydroxyphenyl) propionate] pentaerythritol ester, high-speed stirring and mixing for 10 minutes .
[0044] (3) Put the obtained mixture into a twin-screw extruder and extrude it, and granulate it to obtain a fully biodegradable masterbatch 1. The temperature of each zone of the twin-screw extruder is: 150°C in the first zone, 160°C in the second zone, and 160°C in the third zone 170°C, 175°C in the fourth zone, 175°C in the fifth zone, 170°C in the sixth zone, 165°C in t...
Embodiment 2
[0047] (1) Dry PBSA (blown film grade, Anqing Hexing Company) in a blast oven at 80°C for 6 hours, and dry talc powder (3000 mesh) in a blast oven at 120°C for 5 hours.
[0048] (2) Take 60 parts of talcum powder, add it to the high mixer, stir at low speed, spray 1 part of silane coupling agent KH560 while stirring, then stir at high speed for 5 minutes, then add 40 parts of PBSA and 3 parts of compatibilizer ADR -4370 (manufactured by BASF), 0.1 part of white oil, 0.5 part of antioxidant β-(3,5-di-tert-butyl-4-hydroxyphenyl) octadecyl propionate, stirred and mixed at high speed for 5 minutes.
[0049](3) Put the obtained mixture into a twin-screw extruder and extrude it, and granulate it to obtain fully biodegradable masterbatch 2. The temperature of each zone of the twin-screw extruder is: 90°C in the first zone, 110°C in the second zone, and 110°C in the third zone 120°C, 130°C in the fourth zone, 140°C in the fifth zone, 150°C in the sixth zone, 155°C in the head; the scr...
Embodiment 3
[0052] (1) Dry PBAT (blown film grade, BASF) in a blast oven at 70°C for 10 hours, and dry titanium dioxide (800 mesh) in a blast oven at 110°C for 8 hours.
[0053] (2) Take 70 parts of titanium dioxide, add it to the high-speed mixer, stir at low speed, spray 1.5 parts of titanate coupling agent isopropyl triisostearyl titanate while stirring, then stir at high speed for 10 minutes, and then Add 30 parts of PBAT, 1.5 parts of compatibilizer ADR-4370 (manufactured by BASF), 0.3 parts of calcium stearate, 0.3 parts of antioxidant 2-methylenebis(4-methyl-6-tert-butylphenol ), stirring at high speed for 10 min.
[0054] (3) Put the obtained mixture into a twin-screw extruder and extrude it, and granulate it to obtain fully biodegradable masterbatch 3. The temperature of each zone of the twin-screw extruder is: 90°C in the first zone, 110°C in the second zone, and 110°C in the third zone 120°C, 130°C in the fourth zone, 140°C in the fifth zone, 150°C in the sixth zone, 155°C in ...
PUM
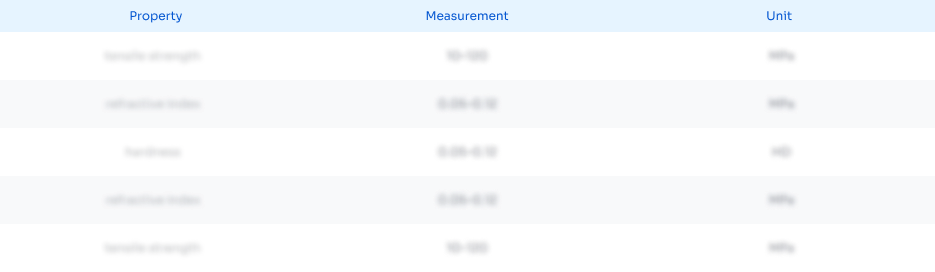
Abstract
Description
Claims
Application Information

- R&D
- Intellectual Property
- Life Sciences
- Materials
- Tech Scout
- Unparalleled Data Quality
- Higher Quality Content
- 60% Fewer Hallucinations
Browse by: Latest US Patents, China's latest patents, Technical Efficacy Thesaurus, Application Domain, Technology Topic, Popular Technical Reports.
© 2025 PatSnap. All rights reserved.Legal|Privacy policy|Modern Slavery Act Transparency Statement|Sitemap|About US| Contact US: help@patsnap.com