Static state calibration device and method for machine visual surface detection equipment
A static calibration and surface detection technology, applied in the field of measurement, can solve the problems of roughly observing the imaging effect of the camera, the difficulty of precise adjustment of the camera, and the lack of matching adjustment devices and methods for the light source and the camera, so as to achieve the effect of ensuring the calibration accuracy
- Summary
- Abstract
- Description
- Claims
- Application Information
AI Technical Summary
Problems solved by technology
Method used
Image
Examples
Embodiment approach 1
[0083] Such as Figure 4 , Figure 5 As shown, align the center line of the ruler 1 with the imaging position of the selected collected sample and put it in place. According to the previously designed imaging angle of the light source, adjust the angle adjustment device 5 to reach the preset angle, turn on the laser emitter 4, and the emitter will emit Create a parallel laser line, adjust the light source according to the pre-designed height of the light source and make the center position of the light source coincide with the laser line, adjust the level, and complete the determination of the angular position of the light source.
[0084] The determination of the angular position of the camera box is consistent with the light source method.
[0085] After the angle adjustment, the matching imaging between the light source and the camera is basically achieved. In order to further adjust the camera imaging effect, the three movable calibration modules 2 on the scale 1 are resp...
Embodiment approach 2
[0087] The device of this patent invention can be used to calibrate the calibration problem when multiple cameras are used together, that is, to adjust the collinear problem of the imaging positions of multiple cameras. Such as Figure 8 As shown, the length of the ruler is appropriately extended according to the field imaging width, and the position of the calibration module is adjusted so that it is located at the head, tail and middle of a camera respectively, and the real-time images collected by two adjacent cameras are respectively observed. The degree and number of thick and thin solid lines can determine whether the camera imaging is on the same straight line, and properly adjust the micro-angle of the camera to achieve the purpose of multiple cameras collinear.
[0088]The implementation of the technical solution of the present invention can accurately locate the imaging position of the light source and the camera, and quickly and accurately adjust the micro-angle of ...
PUM
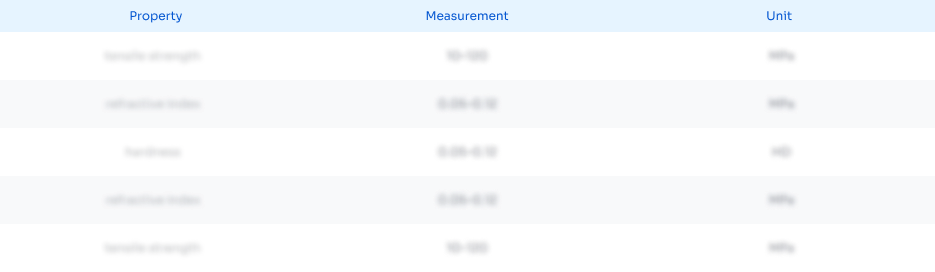
Abstract
Description
Claims
Application Information

- R&D
- Intellectual Property
- Life Sciences
- Materials
- Tech Scout
- Unparalleled Data Quality
- Higher Quality Content
- 60% Fewer Hallucinations
Browse by: Latest US Patents, China's latest patents, Technical Efficacy Thesaurus, Application Domain, Technology Topic, Popular Technical Reports.
© 2025 PatSnap. All rights reserved.Legal|Privacy policy|Modern Slavery Act Transparency Statement|Sitemap|About US| Contact US: help@patsnap.com