Method for producing high-grade fluorite concentrate through multistage discharge flotation method
A high-grade, flotation technology, applied in flotation, solid separation and other directions, can solve the problems of low proportion of high-grade fluorite concentrate, low grade of fluorite concentrate, coarse grinding process, etc. The process is simple, avoiding the deterioration of the selected environment, and reducing the effect of site construction
- Summary
- Abstract
- Description
- Claims
- Application Information
AI Technical Summary
Problems solved by technology
Method used
Examples
Embodiment 1
[0022] Using 50% CaF2-containing fluorite ore from a certain place in Guizhou Province as raw material, with a silicate content of 12% and a carbonate content of 15%, this technological process is used for production, and the product meets the design requirements. The technological process is as follows:
[0023] a. In the pretreatment process, before the pulp enters roughing, according to the content of CaF2, silicate and carbonate in the raw ore, the pH value of the pulp is adjusted to 8-10, and the optimum water temperature is controlled at 20°C-25 At the same time, inject inhibitors and collectors in stages to control the dosage of inhibitors and collectors.
[0024] b. In the roughing process, use a flotation machine with four or five slots for roughing, and further improve the flotation machine, reduce the speed of the motor in the last slot of the flotation machine, Use an 8-stage motor to replace the original 6-stage motor, and at the same time close the intake pipe of...
Embodiment 2
[0030] Using fluorite ore containing 25% CaF2 in a certain place in Guangxi as raw material, its carbonate content is 30%, and its silicate content is 22%. It is produced by this technological process, and the product meets the design requirements. The technological process is as follows:
[0031] Select the flotation machine with five grooves for use as the roughing equipment, select the flotation machine with three grooves for use as the fine selection equipment, the improvement of the flotation equipment is the same as that of embodiment 1, the motor of the last groove of the flotation machine is reduced Speed, replace the original 6-stage motor with an 8-stage motor, and close the intake pipe of the last slot at the same time.
[0032] The CaF2 grade of the raw ore is 25%, the carbonate content is 30%, and the silicate content is 22%. The second inhibitor should be added in the roughing process. All the other methods are the same as in Example 1.
[0033] This technical p...
PUM
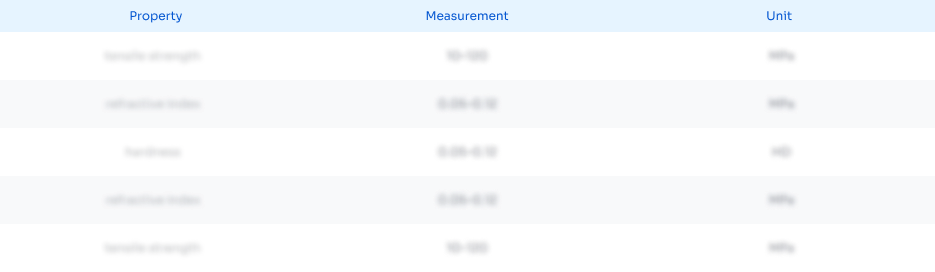
Abstract
Description
Claims
Application Information

- R&D
- Intellectual Property
- Life Sciences
- Materials
- Tech Scout
- Unparalleled Data Quality
- Higher Quality Content
- 60% Fewer Hallucinations
Browse by: Latest US Patents, China's latest patents, Technical Efficacy Thesaurus, Application Domain, Technology Topic, Popular Technical Reports.
© 2025 PatSnap. All rights reserved.Legal|Privacy policy|Modern Slavery Act Transparency Statement|Sitemap|About US| Contact US: help@patsnap.com