Stiffness frequency adjustable two-dimensional micro-motion platform based on stress stiffening principle
A two-dimensional micro-motion and frequency adjustment technology, which is applied to large fixed members, machine tool parts, feeding devices, etc., can solve problems such as complex motion control, inconsistent displacement amplification factors of the motion platform, and difficulty in meeting the needs of high-speed and precise motion. The effect of simple control, reduced motion inertia, and improved performance
- Summary
- Abstract
- Description
- Claims
- Application Information
AI Technical Summary
Problems solved by technology
Method used
Image
Examples
Embodiment Construction
[0031] The technical solutions of the present invention will be further described below in conjunction with the accompanying drawings and through specific implementation methods.
[0032] Such as Figure 1 to Figure 3 The shown two-dimensional micro-motion platform with adjustable stiffness and frequency based on the principle of stress stiffening includes an X-direction film group 201, a Y-direction film group 202, an X-direction motion sub-platform 203, a Y-direction motion sub-platform 204, and an outer frame 205 , X-direction drive, Y-direction drive, X-direction displacement sensor 8, Y-direction displacement sensor 10, frame 1 and working platform 5;
[0033] The outer frame 205 is fixed on the frame 1; the elastic X-direction film group 201 is arranged on both sides of the X-direction movement sub-platform 203, one end of which is connected to the inner wall of the outer frame 205, and the other One end is connected to the X-direction movement sub-platform 203; the ela...
PUM
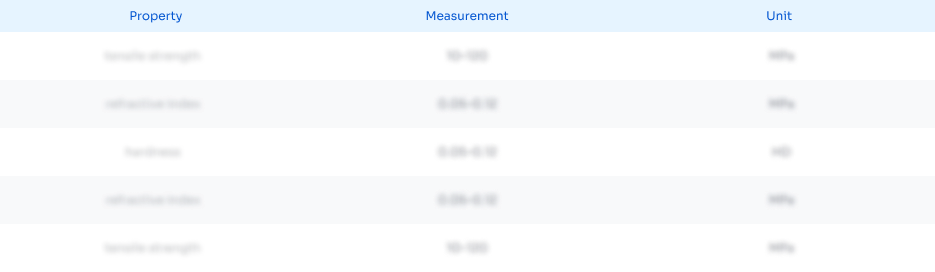
Abstract
Description
Claims
Application Information

- Generate Ideas
- Intellectual Property
- Life Sciences
- Materials
- Tech Scout
- Unparalleled Data Quality
- Higher Quality Content
- 60% Fewer Hallucinations
Browse by: Latest US Patents, China's latest patents, Technical Efficacy Thesaurus, Application Domain, Technology Topic, Popular Technical Reports.
© 2025 PatSnap. All rights reserved.Legal|Privacy policy|Modern Slavery Act Transparency Statement|Sitemap|About US| Contact US: help@patsnap.com