An in-situ measurement method for large-scale flatness
A measurement method and flatness technology, which are applied in the field of high-precision measurement of large-scale flatness and high-precision in-situ detection of large-scale flatness during processing, which can solve problems such as low measurement efficiency, inability to meet detection tasks and measurement problems. , to achieve the effect of high measurement accuracy, saving detection cost and fast sampling time
- Summary
- Abstract
- Description
- Claims
- Application Information
AI Technical Summary
Problems solved by technology
Method used
Image
Examples
Embodiment Construction
[0025] Various details involved in the technical solution of the present invention will be described in detail below in conjunction with the accompanying drawings. It should be noted that the described embodiments are only intended to facilitate the understanding of the present invention, and do not serve as any limitation.
[0026] Such as figure 1 It shows the large-scale flatness high-precision in-situ measurement method based on the dual-station laser tracker of the present invention. This method is based on the spherical coordinate principle of the laser tracker and the high-precision distance measurement characteristics. Using the measurement data of one station to perform error compensation on the measurement data of the other station, so as to improve the flatness measurement accuracy. The embodiment of the inventive method is as follows: the method is completed through the following steps:
[0027] Step S2: Arrange two laser trackers near the measured plane 3, and t...
PUM
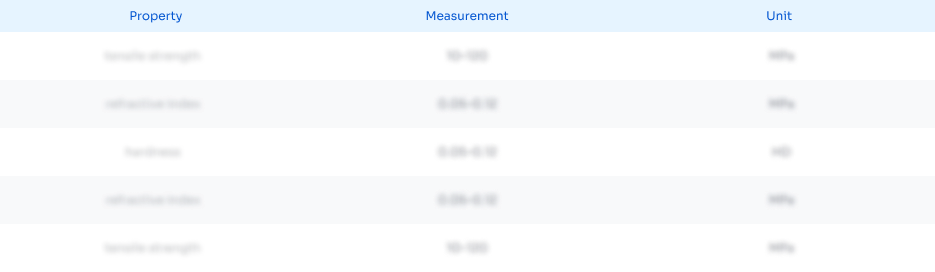
Abstract
Description
Claims
Application Information

- R&D Engineer
- R&D Manager
- IP Professional
- Industry Leading Data Capabilities
- Powerful AI technology
- Patent DNA Extraction
Browse by: Latest US Patents, China's latest patents, Technical Efficacy Thesaurus, Application Domain, Technology Topic, Popular Technical Reports.
© 2024 PatSnap. All rights reserved.Legal|Privacy policy|Modern Slavery Act Transparency Statement|Sitemap|About US| Contact US: help@patsnap.com