Electro-hydraulic position servo driver and its driving method based on dsp
A technology of electro-hydraulic position servo and driving method, which is applied in the direction of fluid pressure actuation device, fluid pressure actuation system components, mechanical equipment, etc. The effect of expanding the scope of application and reducing the burden
- Summary
- Abstract
- Description
- Claims
- Application Information
AI Technical Summary
Problems solved by technology
Method used
Image
Examples
specific Embodiment approach 1
[0028] Specific implementation mode one: combine figure 1 Describe this embodiment, the DSP-based electro-hydraulic position servo driver described in this embodiment includes DSP circuit 1, FPGA circuit 2, position sensor interface circuit 3, power amplifier circuit 4, AD conversion and DA conversion circuit 5 and communication circuit 6 The communication circuit 6 is used to realize the data transmission between the DSP circuit 1 and the upper computer or the control bus; the position sensor interface circuit 3 is used to send the position signal of the differential sensor to the FPGA circuit 2; After processing, it is sent to DSP circuit 1; power amplifier circuit 4 is used to amplify the control quantity sent by DSP circuit 1, and then drives the electro-hydraulic valve; AD conversion and DA conversion circuit 5 is used to convert the analog signal sent from outside After being converted into a digital signal, it is sent to the DSP circuit 1, or the digital control signal ...
specific Embodiment approach 2
[0032] Embodiment 2: This embodiment is a further limitation of the DSP-based electro-hydraulic position servo driver described in Embodiment 1. In this embodiment, the DSP circuit 1 is embedded with a self-calibration module implemented by software. Includes the following units:
[0033] Dead zone parameter estimation unit: every time t, measure the dead zone width of the system, and start the dead zone parameter updating unit and the control system modeling unit at the same time after the end of the unit;
[0034] Dead zone parameter command update unit: send the measured dead zone width as a new dead zone parameter command to the power amplifier circuit 4;
[0035] Control system modeling unit: establish the open-loop transfer function of the proportional valve position control system, and start the control parameter calculation unit after the unit ends;
[0036] Control parameter calculation unit: calculate system control parameters according to the open-loop transfer fun...
specific Embodiment approach 3
[0042] Specific Embodiment 3: This embodiment is a further limitation of the DSP-based electro-hydraulic position servo driver described in Embodiment 2. In this embodiment, the control system modeling unit establishes the open loop of the proportional valve position control system For the transfer function, the initial open-loop transfer function is obtained by calculating the preset system parameters, and the open-loop transfer function in the cycle process is obtained by calculating the identification parameters.
PUM
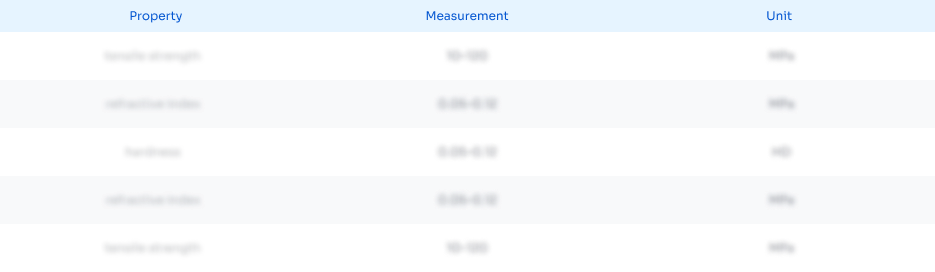
Abstract
Description
Claims
Application Information

- R&D
- Intellectual Property
- Life Sciences
- Materials
- Tech Scout
- Unparalleled Data Quality
- Higher Quality Content
- 60% Fewer Hallucinations
Browse by: Latest US Patents, China's latest patents, Technical Efficacy Thesaurus, Application Domain, Technology Topic, Popular Technical Reports.
© 2025 PatSnap. All rights reserved.Legal|Privacy policy|Modern Slavery Act Transparency Statement|Sitemap|About US| Contact US: help@patsnap.com