A Nickel-Based Superalloy With Excellent Performance Against Molten Salt Corrosion
A nickel-based superalloy and molten salt corrosion technology, which is applied in the field of nickel-based superalloys, can solve the problems of high durability and low performance of fluoride corrosion-resistant alloys, and achieve high temperature structure stability, excellent room temperature plasticity, and good corrosion resistance. Effect of Molten Salt Corrosion Properties
- Summary
- Abstract
- Description
- Claims
- Application Information
AI Technical Summary
Problems solved by technology
Method used
Image
Examples
Embodiment 1
[0027] The composition of the alloy (No.1 alloy) in this example is shown in Table 2. After vacuum induction melting (melting 20 kg ingot shape), the composition alloy is cast into an ingot, and then forged into bar. The forged bar is heat treated, and the heat treated test bar is processed into a performance test sample and a corrosion test sample, and then the durability test and the corrosion test are carried out. The test results are shown in Table 3 and Table 4.
[0028] Table 2 Example 1-11 alloy composition, wt%
[0029] alloy Cr Fe Mo Ti Ta Nb C Si mn Ni No.1 6.2 3.8 12.5 1.2 0.3 0 0.032 0.48 0.67 Remain No.2 7.0 4.3 14.2 1.8 0.1 0.1 0.042 0.48 0.67 Remain No.3 7.9 4.8 14.2 1.0 0.5 0.5 0.048 0.49 0.71 Remain No.4 7.0 4.3 14.2 0.5 1.3 0.15 0.042 0.48 0.67 Remain No.5 7.9 4.8 15.2 0.5 0.8 0.7 0.058 0.68 0.77 Remain No.6 7.0 4.1 16.2 0.1 1.9 0 0.058 0.6...
Embodiment 2
[0031] The composition of the alloy (No.2 alloy) in this example is shown in Table 2. After vacuum induction melting (melting 20 kg ingot shape), the composition alloy is cast into an ingot, and then forged into bar. The forged bar is heat treated, and the heat treated test bar is processed into a performance test sample and a corrosion test sample, and then the durability test and the corrosion test are carried out. The test results are shown in Table 3 and Table 4.
Embodiment 3
[0033] The composition of the alloy (No.3 alloy) in this example is shown in Table 2. After vacuum induction melting (melting 20 kg ingot shape), the composition alloy is cast into an ingot, and then forged into bar. The forged bar is heat treated, and the heat treated test bar is processed into a performance test sample and a corrosion test sample, and then the durability test and the corrosion test are carried out. The test results are shown in Table 3 and Table 4.
PUM
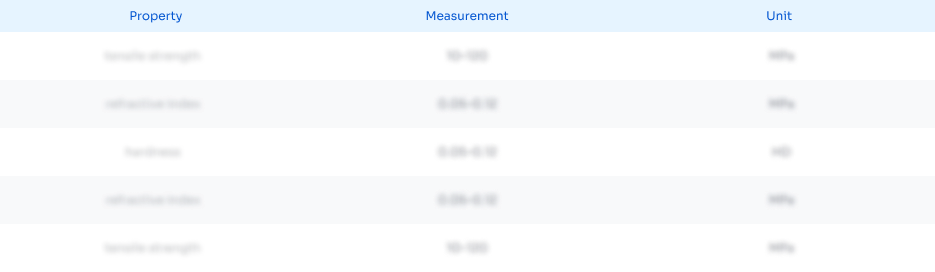
Abstract
Description
Claims
Application Information

- R&D Engineer
- R&D Manager
- IP Professional
- Industry Leading Data Capabilities
- Powerful AI technology
- Patent DNA Extraction
Browse by: Latest US Patents, China's latest patents, Technical Efficacy Thesaurus, Application Domain, Technology Topic, Popular Technical Reports.
© 2024 PatSnap. All rights reserved.Legal|Privacy policy|Modern Slavery Act Transparency Statement|Sitemap|About US| Contact US: help@patsnap.com