Treatment method of blast furnace central conical section throat and its wear-resistant structure
A processing method and a cone section technology, applied to blast furnaces, blast furnace details, blast furnace parts, etc., can solve problems such as the gap between the maintenance period of the central cone section throat and the lower related equipment, waste of raw materials, and reduced production volume. Achieve the effects of improving the effect of wetting connection, guaranteeing service life and prolonging service life
- Summary
- Abstract
- Description
- Claims
- Application Information
AI Technical Summary
Problems solved by technology
Method used
Image
Examples
Embodiment Construction
[0029] Such as figure 1 , figure 2 Shown is a blast furnace central conical throat pipe with strong wear resistance and long service life provided by the present invention, and a treatment method for the wear-resistant structure of the blast furnace central conical throat pipe. The blast furnace central conical throat includes a blast furnace central conical throat substrate 1, and the inner surface of the blast furnace central conical throat substrate 1 is covered with a wear-resistant cladding layer 2 and a wear-resistant installation layer 3. The wear-resistant structure 4, the wear-resistant cladding layer 2 covers the wear-resistant installation layer 3 and the inner side wall of the blast furnace central cone section throat substrate 1 without the wear-resistant installation layer 3 . In order to further improve the connection effect between the wear-resistant installation layer 3 and the blast furnace center cone section throat substrate 1, and simultaneously improve...
PUM
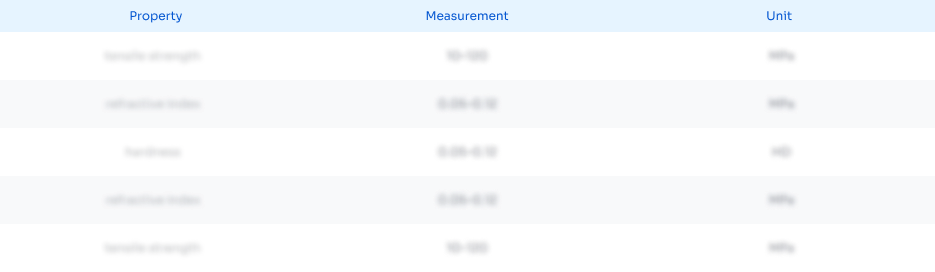
Abstract
Description
Claims
Application Information

- R&D Engineer
- R&D Manager
- IP Professional
- Industry Leading Data Capabilities
- Powerful AI technology
- Patent DNA Extraction
Browse by: Latest US Patents, China's latest patents, Technical Efficacy Thesaurus, Application Domain, Technology Topic.
© 2024 PatSnap. All rights reserved.Legal|Privacy policy|Modern Slavery Act Transparency Statement|Sitemap