Cutting parameter determining method for combined machining of cutting tool and high-temperature alloy
A high-temperature alloy and cutting tool technology, which is applied in the direction of electrical digital data processing, special data processing applications, instruments, etc., can solve problems such as difficult selection of cutting parameters, low cutting efficiency, and tool wear
- Summary
- Abstract
- Description
- Claims
- Application Information
AI Technical Summary
Problems solved by technology
Method used
Image
Examples
Embodiment Construction
[0011] In order to realize the purpose of improving cutting efficiency and reducing tool wear, the present invention adopts the following methods:
[0012] Step 1: Based on the Archard model in the tool model of the adhesive wear theory, according to the geometric relationship between the tool and the workpiece in the process of cutting the superalloy workpiece, the adhesive wear change dW is Based on this, the establishment of the wear model of the flank face of cutting superalloy tools
[0013] Step 2: According to the tool flank wear model, determine the relationship between the normal pressure on the tool wear surface and the cutting temperature when the tool cuts the superalloy workpiece with the minimum adhesive wear: P=f(θ);
[0014] Step 3: Determine the relationship between the yield strength of the superalloy workpiece and the cutting temperature σ s =f(θ);
[0015] Step Four: In Take the minimum value that is , the cutting temperature θ corresponding to the...
PUM
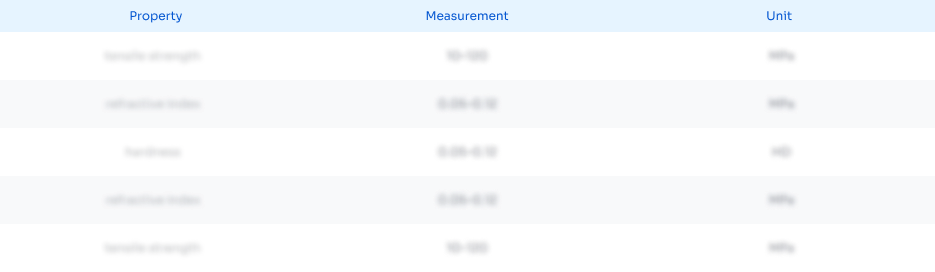
Abstract
Description
Claims
Application Information

- R&D Engineer
- R&D Manager
- IP Professional
- Industry Leading Data Capabilities
- Powerful AI technology
- Patent DNA Extraction
Browse by: Latest US Patents, China's latest patents, Technical Efficacy Thesaurus, Application Domain, Technology Topic, Popular Technical Reports.
© 2024 PatSnap. All rights reserved.Legal|Privacy policy|Modern Slavery Act Transparency Statement|Sitemap|About US| Contact US: help@patsnap.com