Integrated modification method for reducing pollutant emission of circulating fluidized bed boiler
A pollutant emission and circulating fluidized bed technology, which is applied in the direction of fluidized bed combustion equipment, combustion methods, and fuels burned in a molten state, can solve the problems of large initial investment in equipment, long transformation period, and increased operating costs of enterprises. To achieve the effects of short transformation period, low risk and avoiding equipment investment
- Summary
- Abstract
- Description
- Claims
- Application Information
AI Technical Summary
Problems solved by technology
Method used
Image
Examples
Embodiment 1
[0081] Such as Figure 1 ~ Figure 4 , involving a 480t / h circulating fluidized bed boiler. The boiler before the renovation includes a furnace dense-phase zone 1 and a furnace dilute-phase zone 2. There are 6 furnace inner panel heating surfaces A (left and right sides) in the furnace dilute-phase zone 2 3 pieces each for the walls). Furnace dilute-phase area 2 is connected with separator BA through separator inlet flue B1. There are 2 separators BA in total. The flue gas after separator dust removal enters the tail flue 5 through separator center tube B4. Road heating surface 6, the flue gas is discharged after cooling.
[0082] The combustion temperature in the dense phase zone 1 of the furnace before the transformation is 920°C, the temperature of each point in the dense phase zone 1 of the furnace is 780-1050°C, the differential pressure in the middle of the furnace is 1.2kPa, the differential pressure in the upper part of the furnace is 0.4kPa, and the SO in the flue gas...
Embodiment 2
[0092] see Figure 14 , involving a 1024t / h circulating fluidized bed boiler. The boiler before the renovation includes a furnace dense-phase zone 1 and a furnace dilute-phase zone 2. In the furnace dilute-phase zone 2, there are 12 furnace inner panel heating surfaces A (left and right sides 6 pieces for each wall), and a total of 3 separators BA.
[0093] The combustion temperature of dense-phase zone 1 of the furnace before the transformation was 940°C, the temperature of each point in the dense-phase zone 1 of the furnace was 800-1080°C, the differential pressure in the middle of the furnace was 1.5kPa, the differential pressure in the upper part of the furnace was 0.6kPa, and the SO in the flue gas 2 The emission concentration is 300~500mg / m 3 , NO x The emission concentration is 210~250mg / m 3 . The total air volume of the boiler is 950000Nm 3 / h, the primary air DP of the boiler is 550000Nm 3 / h, the wind cap C2 adopts a bell-shaped wind cap, the resistance of the ...
PUM
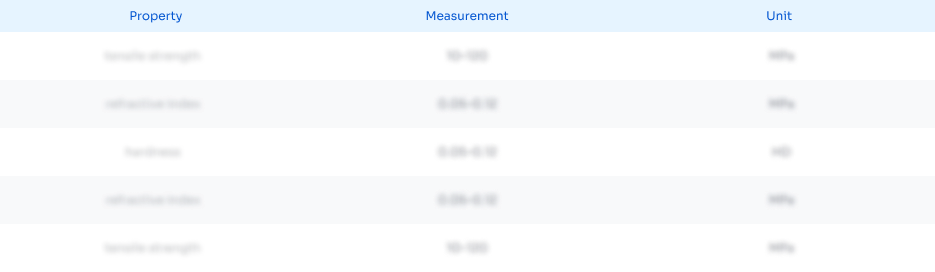
Abstract
Description
Claims
Application Information

- R&D
- Intellectual Property
- Life Sciences
- Materials
- Tech Scout
- Unparalleled Data Quality
- Higher Quality Content
- 60% Fewer Hallucinations
Browse by: Latest US Patents, China's latest patents, Technical Efficacy Thesaurus, Application Domain, Technology Topic, Popular Technical Reports.
© 2025 PatSnap. All rights reserved.Legal|Privacy policy|Modern Slavery Act Transparency Statement|Sitemap|About US| Contact US: help@patsnap.com