Upper arm of robot
A robot and upper arm technology, applied in the field of robotics, can solve the problems affecting the flexibility of the robot arm, shorten the service life of the motor, and the timing belt 110 is too long, etc., and achieve the effects of adjustable gear clearance, increased selection range, and simple assembly
- Summary
- Abstract
- Description
- Claims
- Application Information
AI Technical Summary
Problems solved by technology
Method used
Image
Examples
Embodiment
[0036] Such as Figure 2-4 As shown, the upper arm of the robot of the present invention includes a wrist joint power input device and a wrist joint, and the wrist joint power input device includes a fourth joint servo motor 83, a fifth joint servo motor 82, a sixth joint servo motor 80 and a motor protection cover 81 The wrist joint includes the fourth joint reducer 55, the fifth joint reducer 52, the sixth joint reducer 1, the fourth joint power shaft 67, the fifth joint power shaft 64, the sixth joint power shaft 65, the fourth joint power shaft The joint rotating arm 35 , the fifth joint swing arm 54 and the end mechanical flange 2 , the fifth joint power shaft 64 is set in the sixth joint power shaft 65 , and the sixth joint power shaft 65 is set in the fourth joint power shaft 67 . This structure solves the input power distribution problem of the fourth, fifth and sixth joints at the end of the industrial robot.
[0037] In the wrist power input device:
[0038] The ou...
PUM
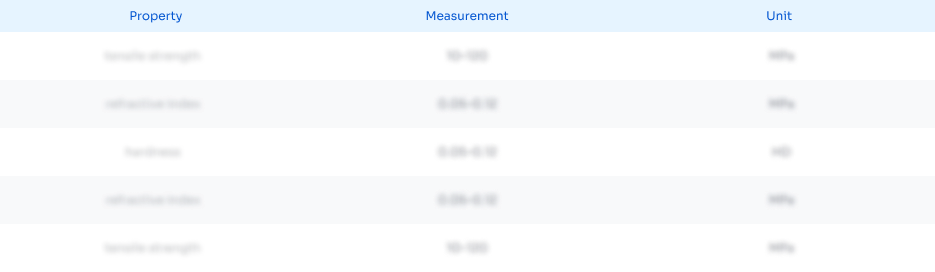
Abstract
Description
Claims
Application Information

- Generate Ideas
- Intellectual Property
- Life Sciences
- Materials
- Tech Scout
- Unparalleled Data Quality
- Higher Quality Content
- 60% Fewer Hallucinations
Browse by: Latest US Patents, China's latest patents, Technical Efficacy Thesaurus, Application Domain, Technology Topic, Popular Technical Reports.
© 2025 PatSnap. All rights reserved.Legal|Privacy policy|Modern Slavery Act Transparency Statement|Sitemap|About US| Contact US: help@patsnap.com