Design method of position and attitude observer for airborne parallel platform
A design method and observer technology, applied in instruments, computing, manipulators, etc., can solve the problem of expensive sensors
- Summary
- Abstract
- Description
- Claims
- Application Information
AI Technical Summary
Problems solved by technology
Method used
Image
Examples
Embodiment Construction
[0014] The present invention will be described in further detail below in conjunction with the accompanying drawings.
[0015] The present invention takes the six-degree-of-freedom parallel platform carried by the machine (vehicle) as the research object (such as figure 1 Shown), its fixed platform ④ is fixed on the locomotive (vehicle) body. Since the body has a certain pose during the movement process and cannot always be kept horizontal, the pose of the fixed platform of the machine (vehicle) borne parallel platform is dynamically changed, which is different from the static parallel platform in the past. The position of the worktable is controlled by six parallel telescopic rods ② and universal hinge ① to ensure that the work platform ③ is always in a horizontal state, so that the load posture remains stable during operation.
[0016] (1) Considering the characteristics of the actual system, establish a dynamic model of the airborne platform
[0017] a. First, fully consi...
PUM
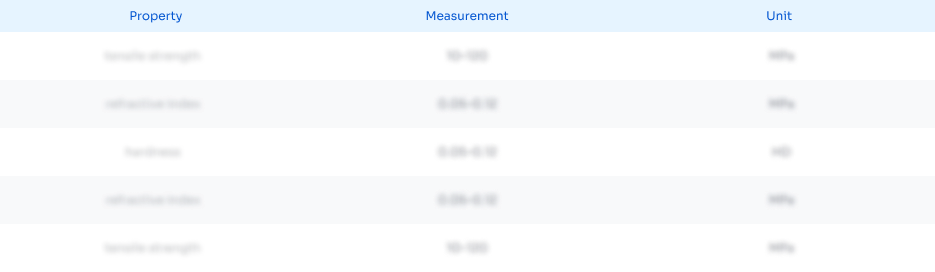
Abstract
Description
Claims
Application Information

- R&D
- Intellectual Property
- Life Sciences
- Materials
- Tech Scout
- Unparalleled Data Quality
- Higher Quality Content
- 60% Fewer Hallucinations
Browse by: Latest US Patents, China's latest patents, Technical Efficacy Thesaurus, Application Domain, Technology Topic, Popular Technical Reports.
© 2025 PatSnap. All rights reserved.Legal|Privacy policy|Modern Slavery Act Transparency Statement|Sitemap|About US| Contact US: help@patsnap.com