A laser displacement sensor calibration device
A calibration device, laser displacement technology, applied in the direction of using optical devices, measuring devices, instruments, etc., can solve the problem of doubts about the accuracy of measurement results, avoid human measurement errors, improve work efficiency and convenience of use, and improve measurement. The effect of precision
- Summary
- Abstract
- Description
- Claims
- Application Information
AI Technical Summary
Problems solved by technology
Method used
Image
Examples
Embodiment Construction
[0010] The best embodiment of the present invention will be described in detail below with reference to the accompanying drawings.
[0011] Such as figure 1 As shown, the laser displacement sensor verification device of the preferred embodiment of the present invention includes: a main body 1, a light transmission port 2, a magnet 3, a conversion button 4, a positioning magnet 5, a positioning stopper 6, a laser reflection plate 7, a rotating shaft 8 and a box Body 9. The main body 1 is made of thin-plate stainless steel with a small deformation coefficient to ensure that the installation position between the rotating shafts 8 where the five laser reflectors 7 are installed does not change with the external environmental conditions. For example, the expansion rate of 3Cr13 is 12%, and the expansion rate of 0Cr26Ni5Mo2 is 18%. The expansion rate of 00Cr18Ni5Mo3Si2 is 20%, and the expansion rate of 0Cr13Al is 20%. The smaller the expansion rate, the smaller the deformation unde...
PUM
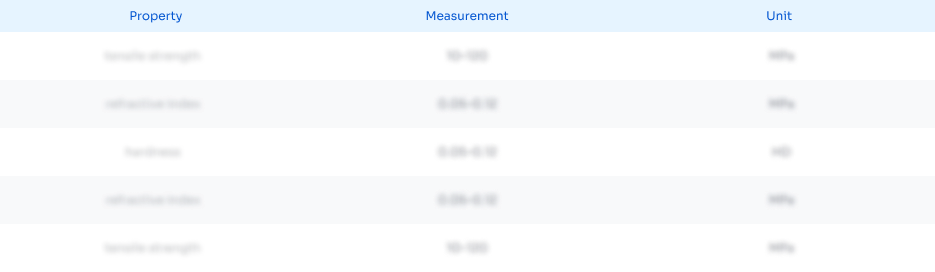
Abstract
Description
Claims
Application Information

- R&D
- Intellectual Property
- Life Sciences
- Materials
- Tech Scout
- Unparalleled Data Quality
- Higher Quality Content
- 60% Fewer Hallucinations
Browse by: Latest US Patents, China's latest patents, Technical Efficacy Thesaurus, Application Domain, Technology Topic, Popular Technical Reports.
© 2025 PatSnap. All rights reserved.Legal|Privacy policy|Modern Slavery Act Transparency Statement|Sitemap|About US| Contact US: help@patsnap.com