Underframe structure of a rail vehicle body
A rail vehicle and underframe technology, which is applied to the underframe, railway car body parts, transportation and packaging, etc., can solve the problem that the distance between the traction guide beam and the coupler installation hole becomes larger, the end structure of the underframe cannot meet the technical requirements, and the support Reduced effect and other issues, to achieve the effect of light weight, high strength performance, and easy modular production
- Summary
- Abstract
- Description
- Claims
- Application Information
AI Technical Summary
Problems solved by technology
Method used
Image
Examples
Embodiment 1
[0030] A subway car body underframe structure, such as figure 1 As shown, the coupler installation hole is set on the coupler installation profile 8, and the traction guide beam 9 and the traction beam 6 provide support to bear the longitudinal load transmitted by the coupler. The traction beam cover plate 2, the traction beam seal plate 3, and the coupler installation profile cover plate 4 is welded with the coupler installation profile 8 and the draw beam 6 to form a closed load-bearing structure with good strength and rigidity. The traction beam 6 is connected with the corbel 1, and the reinforcement vertical plate 5 is set in the middle arc section of the traction beam 6 for partial reinforcement, but there is a certain length of distance from the corbel 1, and the open space formed here can be used to install the corbel. 1 Connected bogie structure, the traction wing 7 is arranged on both sides of the coupler installation profile 8, and bears the torsional load transmitte...
Embodiment 2
[0035] Figure 5It is a schematic diagram of the connection of the coupler installation profile of a rail vehicle body chassis structure. The difference from Example 1 is that the coupler installation profile is a structure without a closed cavity, that is, the profile reinforcement rib 8c is cancelled, and the profile vertical plate connection is added. Rib 8f, in order to transfer load better, the profile riser connecting rib 8f is set to correspond to the profile guide beam connecting rib 8a. This structure needs to extend the reinforced vertical plate 5 so that it is connected with the profiled vertical plate connecting rib 8f, and bear the longitudinal force of the profiled coupler mounting plate 8e together with the traction guide beam 9 to disperse the stress on the traction beam 6, When the designed car body bears a longitudinal compression load of 1000kN, all base materials and welds can meet the requirements of relevant standards.
PUM
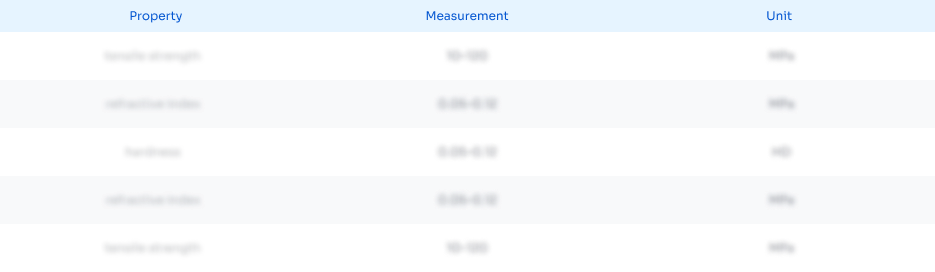
Abstract
Description
Claims
Application Information

- Generate Ideas
- Intellectual Property
- Life Sciences
- Materials
- Tech Scout
- Unparalleled Data Quality
- Higher Quality Content
- 60% Fewer Hallucinations
Browse by: Latest US Patents, China's latest patents, Technical Efficacy Thesaurus, Application Domain, Technology Topic, Popular Technical Reports.
© 2025 PatSnap. All rights reserved.Legal|Privacy policy|Modern Slavery Act Transparency Statement|Sitemap|About US| Contact US: help@patsnap.com