3D (three-dimensional) printing system structure
A system structure and 3D printing technology, applied in the field of 3D printing, can solve problems such as reducing the quality or pass rate of processed parts, limiting the size of processed parts, and affecting processing accuracy, so as to reduce the difficulty of manufacturing and testing, reduce motion modulation, and improve The effect of machining accuracy
- Summary
- Abstract
- Description
- Claims
- Application Information
AI Technical Summary
Problems solved by technology
Method used
Image
Examples
Embodiment Construction
[0026] Examples of the present invention are described below. But the following examples are limited to explain the present invention, and the protection scope of the present invention should include the whole content of claim, and through following embodiment, those skilled in the art can realize the whole content of claim of the present invention.
[0027] Such as figure 1 , figure 2 , image 3 As shown, it is a 3D printing system structure of the present invention, which consists of a printing platform 1, a base 2, a stage 3, and an X, Y-axis transmission mechanism located on the printing platform 1, connecting the printing platform 1 and the base 2 Composition of the Z-axis drive mechanism. The X and Y axis transmission mechanisms are independent and will not interfere with each other during work. X transmission mechanism is made up of X driving shaft 203, the first sliding shaft 213, the second sliding shaft 214, the first driven bearing 209, the second driven bearin...
PUM
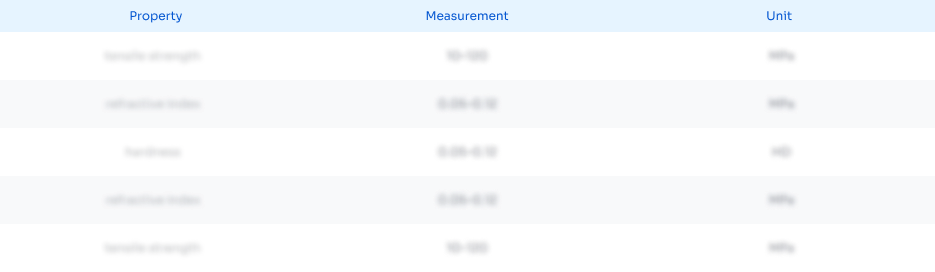
Abstract
Description
Claims
Application Information

- R&D
- Intellectual Property
- Life Sciences
- Materials
- Tech Scout
- Unparalleled Data Quality
- Higher Quality Content
- 60% Fewer Hallucinations
Browse by: Latest US Patents, China's latest patents, Technical Efficacy Thesaurus, Application Domain, Technology Topic, Popular Technical Reports.
© 2025 PatSnap. All rights reserved.Legal|Privacy policy|Modern Slavery Act Transparency Statement|Sitemap|About US| Contact US: help@patsnap.com