Integral type bearing inner tube
An integral bearing technology, applied in textiles and papermaking, etc., can solve the problems of radial unilateral force on the rod and disk, unilateral wear of parts, and limitation of spindle running speed, etc., to achieve uniform radial force on the hole and prolong the service life Life, the effect of reducing the requirements for matching accuracy
- Summary
- Abstract
- Description
- Claims
- Application Information
AI Technical Summary
Problems solved by technology
Method used
Image
Examples
Embodiment Construction
[0008] The present invention will now be described in detail with reference to the embodiments shown in the drawings.
[0009] Such as figure 2 As shown, the integral bearing ingot includes the bearing seat 4, the elastic tube 3, the oil cap 1, the ingot bottom sheet 6, the ingot bottom pad 7, the bushing 5, the ingot bottom pad 7, the ingot bottom sheet 6, and the bushing 5 are installed in sequence In the inner hole at the bottom of the elastic tube 3, the outer circle of the upper end of the elastic tube 3 matches the taper of the inner wall of the bearing seat 4. The inner hole of the bearing seat 4 between the upper end of the elastic tube 3 and the lower end of the oil cap 1 is fitted with a roller with a cage 2.
PUM
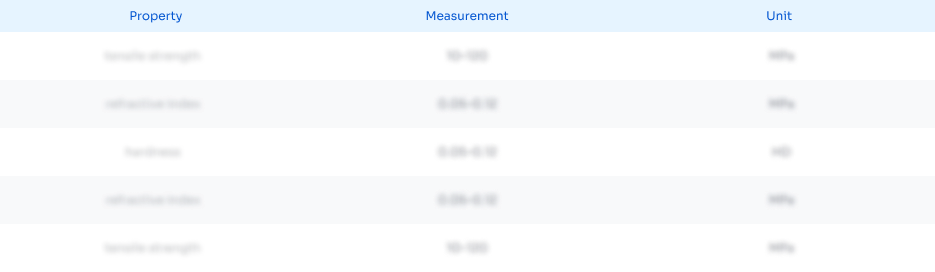
Abstract
Description
Claims
Application Information

- R&D
- Intellectual Property
- Life Sciences
- Materials
- Tech Scout
- Unparalleled Data Quality
- Higher Quality Content
- 60% Fewer Hallucinations
Browse by: Latest US Patents, China's latest patents, Technical Efficacy Thesaurus, Application Domain, Technology Topic, Popular Technical Reports.
© 2025 PatSnap. All rights reserved.Legal|Privacy policy|Modern Slavery Act Transparency Statement|Sitemap|About US| Contact US: help@patsnap.com