Improved braking process for a rail vehicle
A technology of rail vehicle and braking device, which is applied in the direction of operating mechanism of rail vehicle brake, brake, brake, etc. where the braking element interacts with the rail
- Summary
- Abstract
- Description
- Claims
- Application Information
AI Technical Summary
Problems solved by technology
Method used
Image
Examples
Embodiment Construction
[0021] figure 1 A rail vehicle 10 is shown schematically. The rail vehicle 10 has a plurality of cars including a first bogie 12 , a second bogie 14 , a third bogie 16 , and a fourth bogie 18 . Wheel axles 21 , 22 are arranged on the first bogie 12 . Wheel axles 23 , 24 are arranged on the second bogie 14 , wheel axles 25 , 26 are arranged on the bogie 16 and wheel axles 27 , 28 are arranged on the bogie 18 . Pressure-acting brakes, to which brake pressure is supplied via a common control valve, are respectively associated with the wheel axles of the bogies. Thus the first control valve 32 is assigned to the first bogie 12 , the second control valve 34 is assigned to the second bogie 14 , the third control valve 36 is assigned to the third bogie 16 and the fourth control valve 38 is assigned to the fourth bogie shelf. The control valves 32, 34, 36, 38 are connected to main pressure lines which supply control pressure to the control valves 32, 34, 36 and 38. The control v...
PUM
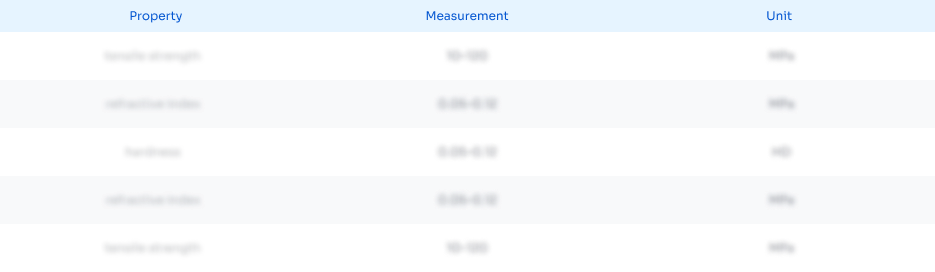
Abstract
Description
Claims
Application Information

- R&D Engineer
- R&D Manager
- IP Professional
- Industry Leading Data Capabilities
- Powerful AI technology
- Patent DNA Extraction
Browse by: Latest US Patents, China's latest patents, Technical Efficacy Thesaurus, Application Domain, Technology Topic, Popular Technical Reports.
© 2024 PatSnap. All rights reserved.Legal|Privacy policy|Modern Slavery Act Transparency Statement|Sitemap|About US| Contact US: help@patsnap.com