Method for preparing industrial ethanol from acetic acid
A technology for industrial ethanol and acetic acid, applied in chemical instruments and methods, preparation of hydroxyl compounds, preparation of organic compounds, etc., can solve the problems of high catalyst cost, harsh reaction conditions, and low single-pass conversion rate, and achieve good technical effects, reaction The effect of mild conditions and low energy consumption
- Summary
- Abstract
- Description
- Claims
- Application Information
AI Technical Summary
Problems solved by technology
Method used
Image
Examples
Embodiment 1
[0030] Weigh 60.0g of 40% silica sol according to the proportion and heat it to 80°C in 1.0L medium water to form solution 1; weigh 121.5g of Cu(NO 3 ) 2 ·3H 2 O, 73.5g Zn(NO 3 ) 2 ·6H 2 O, 10.6g La(NO 3 ) 3 ·6H 2 O, 5.1g Ba(NO 3 ) 2 , 36.8g Al(NO 3 ) 3 9H 2 O, weight percentage is 50%Mn(NO 3 ) 2 Solution 8.2g was dissolved in 1.0L water together, heated and stirred in an 80°C oil bath to form solution 2. Weigh 106.0 g of anhydrous sodium carbonate into a beaker, add distilled water to 1 L, stir and dissolve to prepare a 1.0 mol / L sodium carbonate aqueous solution as solution 3. Solution 2 and solution 3 were added dropwise to solution 1 at the same time, and the pH was kept at about 7.0 to obtain a precipitate, which was filtered to obtain a precipitate. The precipitate was dried and calcined to obtain catalyst 1 (by weight percentage: 40%CuO-20%ZnO%-4%Lal 2 o 3 -5%Al 2 o 3 -3%BaO-4%MnO 2 -24%SiO2 2 )
[0031] Load 50g of the catalyst in the reactor, aft...
Embodiment 2
[0033] Weigh 78.0g of 40% silica sol and 46.7g of 15% aluminum sol in 1.0L medium water and heat to 80°C to form solution 1; weigh a certain amount of 91.13g of Cu(NO 3 ) 2 ·3H 2 O, 73.50g Zn(NO 3 ) 2 ·6H 2 O, 19.4g Co(NO 3 ) 2 ·6H 2 O, 8.54gBa(NO 3 ) 2 , the weight percentage is 50%Mn(NO 3 ) 2 14.4 g of the solution was dissolved in 1.0 L of water, and heated and stirred in an oil bath at 80° C. to form solution 2. Weigh 106 g of anhydrous sodium carbonate into a beaker, add distilled water to 1 L, stir and dissolve to prepare a 1.0 mol / L sodium carbonate aqueous solution as solution 3. Solution 2 and solution 3 were added dropwise to solution 1 at the same time, and the pH was kept at about 7.5 to obtain a precipitate, which was filtered to obtain a precipitate. The precipitate was dried and calcined to obtain catalyst 2 (by weight percentage: 30%CuO-20%ZnO%-5%CoO-7%Al 2 o 3 -5%BaO-7%MnO 2 -31%SiO2 2 )
[0034] Load 50g of the catalyst into the reactor, afte...
Embodiment 3
[0036] Weigh 100g of 40% silica sol and 100g of 15% aluminum sol in 1.3L medium water and heat to 75°C to form solution 1; weigh 75.94g of Cu(NO 3 ) 2 ·3H 2 O, 91.84g Zn(NO 3 ) 2 ·6H 2 O, 19.4g Co(NO 3 ) 2 ·6H 2 O, 2.52gCe(NO 3 ) 2 ·6H 2 O, Ba(NO 3 ) 2 , the weight percentage is 50%Mn(NO 3 ) 2 Solution 14.4g was dissolved in 1.0L water, heated and stirred in an oil bath at 75°C to form solution 2. Weigh 106 g of anhydrous sodium carbonate into a beaker, add distilled water to 1 L, stir and dissolve to prepare a 1.0 mol / L sodium carbonate aqueous solution as solution 3. Solution 2 and solution 3 were added dropwise to solution 1 at the same time, and the pH was kept at about 6.5 to obtain a precipitate, which was filtered to obtain a precipitate. The precipitate was dried and calcined to obtain catalyst 3 (by weight percentage: 25%CuO-25%ZnO%-5%CoO-1%CeO 2 -15%Al 2 o 3 -5%BaO-7%MnO 2 -17%SiO2 2 )
[0037] Load 50g of the catalyst into the reactor, after hyd...
PUM
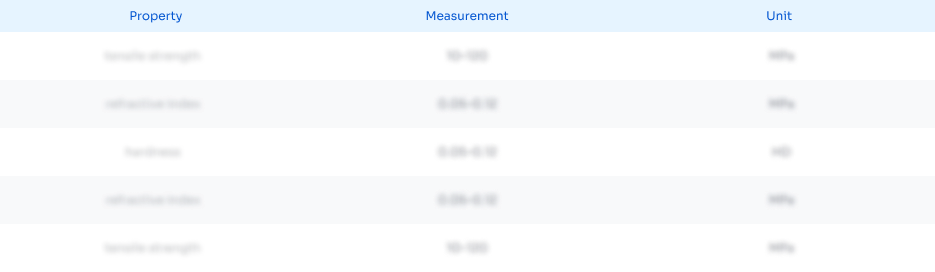
Abstract
Description
Claims
Application Information

- R&D Engineer
- R&D Manager
- IP Professional
- Industry Leading Data Capabilities
- Powerful AI technology
- Patent DNA Extraction
Browse by: Latest US Patents, China's latest patents, Technical Efficacy Thesaurus, Application Domain, Technology Topic, Popular Technical Reports.
© 2024 PatSnap. All rights reserved.Legal|Privacy policy|Modern Slavery Act Transparency Statement|Sitemap|About US| Contact US: help@patsnap.com