Starch type impregnating compound for electronic grade spun yarns
A starch-type sizing agent and electronic-grade technology, which is applied in the field of starch-type sizing agents for electronic-grade spun yarns, can solve the problems of the start-up rate of wire drawing, the hairiness rate of the full bobbin, and the low hairiness rate of the bobbin. The effect of less warping ends, low cop hairiness and high breaking strength
- Summary
- Abstract
- Description
- Claims
- Application Information
AI Technical Summary
Problems solved by technology
Method used
Image
Examples
Embodiment 1
[0028] The starch-type sizing agent used in the production of electronic-grade spun yarn is composed of the following proportioning raw materials (the proportioning ratio of raw materials is the percentage by weight of the sizing agent:
[0029]
[0030]
[0031] The wire drawing process used in this experiment is 1200-1600 hole platinum-rhodium alloy bushing wire drawing. The final raw wire is made of 150-400 monofilaments. The diameter of the single fiber is controlled at 7-9 microns, and the weight of the raw wire is 6-8kg, the conditioning process is 23-25°C, the relative humidity is 55-65%, and the conditioning time is 7.5 hours.
[0032] The test result of this wetting agent embodiment is as follows:
[0033] Test items
Embodiment 2
[0035] The starch-type sizing agent used in the production of electronic-grade spun yarn is composed of the following proportioning raw materials (the proportioning ratio of raw materials is the percentage by weight of the sizing agent:
[0036]
[0037]
[0038] The wire drawing process used in this experiment is 1200-1600 hole platinum-rhodium alloy bushing wire drawing. The final raw wire is made of 150-400 monofilaments. The diameter of the single fiber is controlled at 7-9 microns, and the weight of the raw wire is 6-8kg, the conditioning process is 23-25°C, the relative humidity is 55-65%, and the conditioning time is 7.5 hours.
[0039] The test result of this wetting agent embodiment is as follows:
[0040] Test items
Embodiment 3
[0042] The starch-type sizing agent used in the production of electronic-grade spun yarn is composed of the following proportioning raw materials (the proportioning ratio of raw materials is the percentage by weight of the sizing agent:
[0043]
[0044] The wire drawing process used in this experiment is 1200-1600 hole platinum-rhodium alloy bushing wire drawing. The final raw wire is made of 150-400 monofilaments. The diameter of the single fiber is controlled at 7-9 microns, and the weight of the raw wire is 6-8kg, the conditioning process is 23-25°C, the relative humidity is 55-65%, and the conditioning time is 7.5 hours.
[0045] The test result of this wetting agent embodiment is as follows:
[0046] Test items
PUM
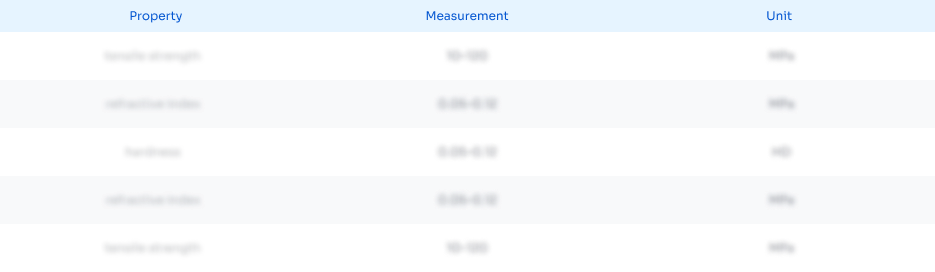
Abstract
Description
Claims
Application Information

- R&D
- Intellectual Property
- Life Sciences
- Materials
- Tech Scout
- Unparalleled Data Quality
- Higher Quality Content
- 60% Fewer Hallucinations
Browse by: Latest US Patents, China's latest patents, Technical Efficacy Thesaurus, Application Domain, Technology Topic, Popular Technical Reports.
© 2025 PatSnap. All rights reserved.Legal|Privacy policy|Modern Slavery Act Transparency Statement|Sitemap|About US| Contact US: help@patsnap.com