High temperature resistant ceramic fiber board
A high-temperature-resistant ceramic and fiberboard technology, applied in the field of ceramic fiber materials, can solve problems such as loss of bonding force and looseness
- Summary
- Abstract
- Description
- Claims
- Application Information
AI Technical Summary
Problems solved by technology
Method used
Examples
Embodiment 1
[0018] Made from the following raw materials in parts by weight:
[0019] 95 parts of aluminum silicate fiber, 2 parts of dispersant and 4 parts of zirconium latex;
[0020] Dispersant composition is Na 2 SiO 3 and CaCO 3 , the composition of zirconium latex is ZrO 2 , Y 2 o 3 and H 2 o 2 .
[0021] Na 2 SiO 3 with CaCO 3 The mass ratio is 2.5:1.
[0022] ZrO 2 with Y 2 o 3 The mass ratio is 95:5, ZrO 2 with H 2 o 2 The mass ratio is 1:4.5.
[0023] The preparation method of the high-temperature-resistant ceramic fiber board: mixing and stirring raw materials, wet vacuum forming, drying processing, drying temperature 120 degrees, time 24 hours, to obtain the product.
Embodiment 2
[0025] Made from the following raw materials in parts by weight:
[0026] 96 parts of aluminum silicate fiber, 1.5 parts of dispersant and 3.5 parts of zirconium latex;
[0027] Dispersant composition is Na 2 SiO 3 and CaCO 3 , the composition of zirconium latex is ZrO 2 , Y 2 o 3 and H 2 o 2 .
[0028] Na 2 SiO 3 with CaCO 3 The mass ratio is 3:1.
[0029] ZrO 2 with Y 2 o 3 The mass ratio is 90:5, ZrO 2 with H 2 o 2 The mass ratio is 1:4.
[0030] The preparation method of the high-temperature-resistant ceramic fiber board: mixing and stirring raw materials, wet vacuum forming, drying processing, drying temperature 110 degrees, time 24 hours, to obtain the product.
Embodiment 3
[0032] Made from the following raw materials in parts by weight:
[0033] 95.5 parts of aluminum silicate fiber, 1 part of dispersant and 3 parts of zirconium latex;
[0034] Dispersant composition is Na 2 SiO 3 and CaCO 3 , the composition of zirconium latex is ZrO 2 , Y 2 o 3 and H 2 o 2 .
[0035] Na 2 SiO 3 with CaCO 3 The mass ratio is 3.5:1.
[0036] ZrO 2 with Y 2 o 3 The mass ratio is 100:5, ZrO 2 with H 2 o 2 The mass ratio is 1:5.
[0037] The preparation method of the high-temperature-resistant ceramic fiberboard includes: mixing and stirring raw materials, wet vacuum forming, and drying processing at a drying temperature of 120 degrees for 22 hours to obtain a product.
PUM
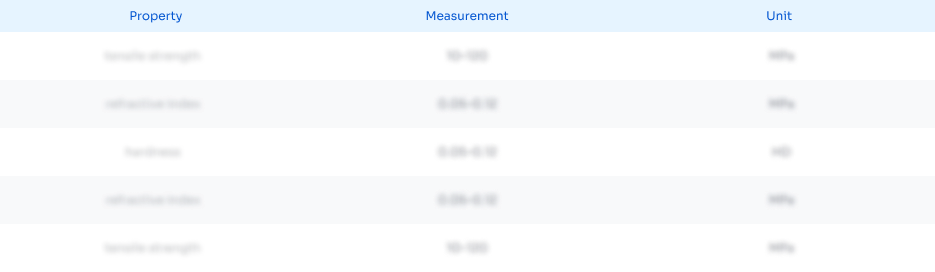
Abstract
Description
Claims
Application Information

- R&D Engineer
- R&D Manager
- IP Professional
- Industry Leading Data Capabilities
- Powerful AI technology
- Patent DNA Extraction
Browse by: Latest US Patents, China's latest patents, Technical Efficacy Thesaurus, Application Domain, Technology Topic, Popular Technical Reports.
© 2024 PatSnap. All rights reserved.Legal|Privacy policy|Modern Slavery Act Transparency Statement|Sitemap|About US| Contact US: help@patsnap.com