A two-degree-of-freedom controllable robot module connection mechanism
A module connection and robot technology, applied in joints, manipulators, manufacturing tools, etc., can solve the problems of complex robot joint structure, insensitive control, poor precision and reliability, etc., and achieve simple structure, strong reliability and high precision Effect
- Summary
- Abstract
- Description
- Claims
- Application Information
AI Technical Summary
Problems solved by technology
Method used
Image
Examples
specific Embodiment approach 1
[0010] Specific implementation mode one: combine figure 1 and figure 2 Describe this embodiment, this embodiment includes the first pitch motor 1, the first motor gear 2, the first pitch spur gear 3, the pitch first gear shaft 4, the pitch pinion 5, the pitch large gear 6, the joint cross shaft 7, Yaw large gear 8, yaw pinion 9, right side frame 10, second pitch motor 11, second motor gear 12, second pitch spur gear 13, second pitch gear shaft 14, first connecting plate 17, second pitching gear Two connecting plates 18, left side frame 19, two first bearing blocks 15 and two second bearing blocks 16, joint cross shaft 7 is provided with horizontal shaft 7-1 and vertical shaft 7-2, horizontal shaft 7-1 One end of the horizontal shaft 7-1 is supported in a first bearing seat 15, and the other end of the horizontal shaft 7-1 passes through the pitch gear 6 and is supported in another first bearing seat 15, and the two first bearing seats 15 are fixed on the left side On the fr...
specific Embodiment approach 2
[0013] Specific implementation mode two: combination figure 2 The present embodiment will be described. In this embodiment, the pitch circle diameter of the first motor gear 2 is equal to the pitch circle diameter of the first pitch spur gear 3 . Other components and connections are the same as those in the first embodiment.
specific Embodiment approach 3
[0014] Specific implementation mode three: combination figure 2 The present embodiment will be described. In this embodiment, the pitch circle diameter of the second motor gear 12 is equal to the pitch circle diameter of the second pitch spur gear 13 . Other components and connections are the same as those in the second embodiment.
PUM
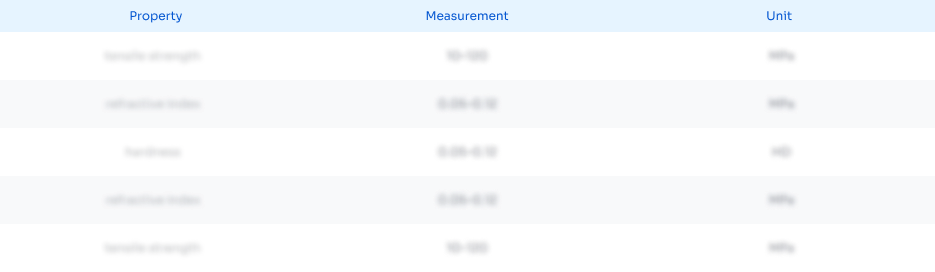
Abstract
Description
Claims
Application Information

- R&D
- Intellectual Property
- Life Sciences
- Materials
- Tech Scout
- Unparalleled Data Quality
- Higher Quality Content
- 60% Fewer Hallucinations
Browse by: Latest US Patents, China's latest patents, Technical Efficacy Thesaurus, Application Domain, Technology Topic, Popular Technical Reports.
© 2025 PatSnap. All rights reserved.Legal|Privacy policy|Modern Slavery Act Transparency Statement|Sitemap|About US| Contact US: help@patsnap.com