Sintering method of optical fiber preform and equipment thereof
A technology for optical fiber preforms and sintering equipment, which is applied in glass manufacturing equipment, manufacturing tools, etc., can solve the problems of inability to adjust temperature in real time and effectively control it.
- Summary
- Abstract
- Description
- Claims
- Application Information
AI Technical Summary
Problems solved by technology
Method used
Image
Examples
Embodiment 1
[0105] Set the temperature required for each stage on the temperature control cabinet 13, then install the powder preform 7 above the quartz suspender 4, send it into the furnace, and sinter according to the sintering method of the preform described above. A laser beam with a wavelength of 850nm and a power of 5.0mw is emitted from the laser transmitter 15, and the signal acquisition unit in the laser control cabinet 24 collects the laser power P' at the receiving end every 5s, and calculates the power difference ΔP =5mw-P'. Here, the upper limit value ΔPmax of ΔP is set to 4.5mw, and the lower limit value ΔPmin of ΔP is set to 3.5mw.
[0106] When the lower tail handle of the preform reaches the horizontal position of the laser, the laser senses the preform and enters the working state. When the ΔP value exceeds ΔPmax, the laser control cabinet sends a signal to the temperature control cabinet 13, requiring it to lower the furnace temperature by 10°C; when the ΔP value is lo...
Embodiment 2
[0108] Set the temperature required for each stage on the temperature control cabinet 13, then install the powder preform 7 above the quartz suspender 4, send it into the furnace, and sinter according to the sintering method of the preform described above. A laser beam with a wavelength of 850nm and a power of 5.0mw is emitted from the laser transmitter 15, and the signal acquisition unit in the laser control cabinet 24 collects the laser power P' at the receiving end every 5s, and calculates the power difference ΔP =5mw-P'. Here, the upper limit value ΔPmax of ΔP is set to 4.2mw, and the lower limit value ΔPmin of ΔP is set to 3.8mw.
[0109] When the lower tail handle of the preform reaches the horizontal position of the laser, the laser senses the preform and enters the working state. When the ΔP value exceeds ΔPmax, the laser control cabinet sends a signal to the temperature control cabinet 13, requiring it to lower the furnace temperature by 5°C; when the ΔP value is low...
PUM
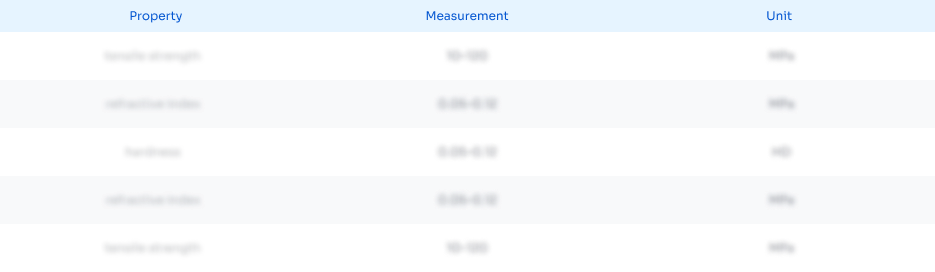
Abstract
Description
Claims
Application Information

- Generate Ideas
- Intellectual Property
- Life Sciences
- Materials
- Tech Scout
- Unparalleled Data Quality
- Higher Quality Content
- 60% Fewer Hallucinations
Browse by: Latest US Patents, China's latest patents, Technical Efficacy Thesaurus, Application Domain, Technology Topic, Popular Technical Reports.
© 2025 PatSnap. All rights reserved.Legal|Privacy policy|Modern Slavery Act Transparency Statement|Sitemap|About US| Contact US: help@patsnap.com