Precise surface polishing device and transmission device for precise surface polishing
A technology of precision polishing and transmission device, which is applied in the direction of grinding drive device, grinding/polishing equipment, grinding machine parts, etc. , Reduce the mechanical failure rate and maintenance cost, and improve the effect of polishing speed
- Summary
- Abstract
- Description
- Claims
- Application Information
AI Technical Summary
Problems solved by technology
Method used
Image
Examples
Embodiment 1
[0030] Please refer to figure 1 This embodiment provides a transmission device for surface precision polishing to drive a processing mechanism to precisely polish a processing object, including a stator mechanism 5, a rotor mechanism 3, and a pendulum mechanism 1. The stator mechanism 5 and the rotor mechanism The magnetic levitation connection is realized between 3, and the rotor mechanism 3 rotates around the axis of the stator mechanism 5 through magnetic levitation. In this embodiment, the rotor mechanism 3 and the stator mechanism 5 have the same axis. Rotating around the axis 51 of the stator mechanism 5, the pendulum mechanism 1 and the rotor mechanism 3 are connected by magnetic levitation, and the pendulum mechanism 1 rotates on its own axis relative to the rotor mechanism 3 through magnetic levitation, that is, around The rotation axis 11 of the pendulum mechanism 1 rotates, the rotation axis 51 of the rotor mechanism 3 and the rotation axis 11 of the pendulum mechanis...
Embodiment 2
[0044] Please refer to image 3 The difference between this embodiment and the first embodiment is that the rotor mechanism 3 is located inside the pendulum mechanism 1, and the stator mechanism 5 is located inside the rotor mechanism 3. Specifically, please refer to Figure 4 , The rotor mechanism 3 is a cylindrical structure, the rotor mechanism 3 is provided with a cylindrical hole 31, the hole 31 penetrates both ends of the rotor mechanism 3, and the axis of the hole 31 is parallel to the The axis of the rotor mechanism 3 does not overlap. In this embodiment, the stator mechanism 5 is arranged in the hole 31. In addition, other technical features of Embodiment 1 can all be applied to Embodiment 3, and this embodiment will not be repeated.
Embodiment 3
[0046] The difference between this embodiment and embodiment 1 is: please refer to Figure 5 with Image 6 The rotor mechanism 3 is a crankshaft structure, and the rotor mechanism 3 is connected to the stator mechanism 5 and the pendulum mechanism 1 through two shaft pins 301 on the crankshaft structure, and the two shaft pins 301 on the crankshaft structure respectively pass The magnetic suspension is connected with the stator mechanism and the pendulum mechanism. Furthermore, the eccentric double rotation similar to embodiment 1 is realized, and the technical effect similar to embodiment 1 is finally realized. This embodiment only lists another specific structure of the rotor mechanism 3, the stator mechanism 5 and the pendulum mechanism 1. The other technical features of Embodiment 1 can also be applied to Embodiment 3. For example, in this embodiment, the shaft pin 301 is also provided with the electromagnetic bearing assembly listed in Embodiment 1. For other features, this...
PUM
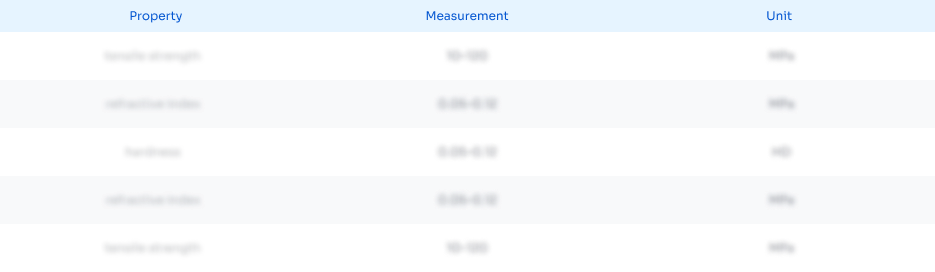
Abstract
Description
Claims
Application Information

- Generate Ideas
- Intellectual Property
- Life Sciences
- Materials
- Tech Scout
- Unparalleled Data Quality
- Higher Quality Content
- 60% Fewer Hallucinations
Browse by: Latest US Patents, China's latest patents, Technical Efficacy Thesaurus, Application Domain, Technology Topic, Popular Technical Reports.
© 2025 PatSnap. All rights reserved.Legal|Privacy policy|Modern Slavery Act Transparency Statement|Sitemap|About US| Contact US: help@patsnap.com