Full-electric plastic injection molding machine
An all-electric, injection machine technology, applied in the field of plastic injection molding, can solve the problems of high manufacturing cost and complex structure of the all-electric plastic injection machine, and achieve the effect of compact structure, large economic potential and low cost
- Summary
- Abstract
- Description
- Claims
- Application Information
AI Technical Summary
Problems solved by technology
Method used
Image
Examples
Embodiment 1
[0041] Example 1: Please refer to the attached figure 1 , which shows a single ball screw cylinder type all-electric plastic injection machine, which includes a single-servo motor injection mechanism and an electric mold clamping mechanism, wherein the single-servo motor injection mechanism includes a servo motor 1, a spindle 11 driven by the servo motor 1, Ball screw barrel, two clutches, injection pusher, ball nut, drive and injection screw. The servo motor drives the main shaft 11 to rotate through the coupling 2, and the main shaft 11 is fixed by two bearings, one is the roller bearing 4 fastened in the center of the end plate 3, and the other is the roller fixed at the end of the ball screw cylinder 12 bearing 16.
[0042] Please refer to the attached figure 2 There are two clutches on the tail of the main shaft, a mobile electromagnetic clutch 5 and a one-way overrunning clutch 6. The mobile electromagnetic clutch 5 includes an electromagnet, an armature 5a and a driv...
Embodiment 2
[0052] Example 2: Please refer to the attached Figure 5-8 , In this embodiment, a double ball screw cylinder structure is adopted, which also includes a servo motor 36 , a main shaft 38 and two ball screw cylinders 50 . The servo motor 36 is fastened on the motor support plate 39 and is linearly connected with the main shaft 38 through a coupling 37 . Main shaft 38 is fixed with roller bearing 40 and roller bearing 53 . Two of the ball screw cylinders 50 are arranged parallel to the main shaft and driven by the main shaft.
[0053] Two clutches are arranged on the main shaft, one is a moving electromagnetic clutch 42 and the other is a one-way overrunning clutch 43. The electromagnet of mobile electromagnetic clutch is fixed on the bottom of clutch assembly cover 41 with screw 42b, and armature 42a is connected with main shaft 38 with key 38a. Key 38a and armature 42a are a sliding fit. The key 38a rotates with the armature 42a, while the armature 42a can slide linearly. ...
PUM
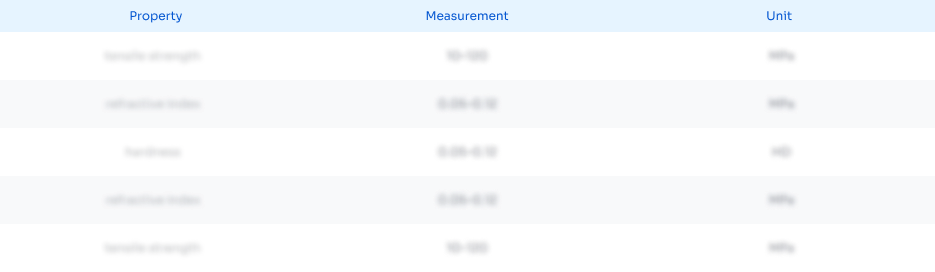
Abstract
Description
Claims
Application Information

- R&D
- Intellectual Property
- Life Sciences
- Materials
- Tech Scout
- Unparalleled Data Quality
- Higher Quality Content
- 60% Fewer Hallucinations
Browse by: Latest US Patents, China's latest patents, Technical Efficacy Thesaurus, Application Domain, Technology Topic, Popular Technical Reports.
© 2025 PatSnap. All rights reserved.Legal|Privacy policy|Modern Slavery Act Transparency Statement|Sitemap|About US| Contact US: help@patsnap.com