Method for producing ethylbenzene and styrene through side chain alkylation of toluene and methanol
A styrene and alkylation technology, applied in the production of ethylbenzene and styrene, can solve the problems of low utilization rate of methanol, easy decomposition of methanol, etc.
- Summary
- Abstract
- Description
- Claims
- Application Information
AI Technical Summary
Problems solved by technology
Method used
Image
Examples
Embodiment 1
[0036] Toluene and a first stream of methanol enter the first reaction zone where they contact the catalyst to produce a first reaction effluent. The first reaction effluent and the second methanol enter the second reaction zone and contact the catalyst to generate the second reaction effluent. The second reaction effluent enters a third reaction zone where it contacts the catalyst to produce a third reaction effluent comprising ethylbenzene and styrene. Ethylbenzene and styrene were separated from the third reaction effluent.
[0037] Wherein, the first reaction zone, the second reaction zone and the third reaction zone are all primary fixed-bed reactors, and the catalysts loaded therein are all KCsX. The temperature in the first reaction zone is 385°C, and the reaction weight hourly space velocity is 2.7 hours -1 , the reaction pressure is 0.1MPa. The temperature in the second reaction zone is 400°C, and the reaction weight hourly space velocity is 3 hours -1 , the react...
Embodiment 2
[0044] Same as [Example 1], except that the operating conditions of each reaction zone are changed, and the catalysts loaded therein are all KCsX. The temperature in the first reaction zone is 380°C, and the reaction weight hourly space velocity is 2.5 hours -1 , the reaction pressure is 0.15MPa. The temperature in the second reaction zone is 400°C, and the reaction weight hourly space velocity is 2.9 hours -1 , the reaction pressure is 0.1MPa. The temperature in the third reaction zone is 410°C, and the reaction weight hourly space velocity is 2.9 hours -1 , the reaction pressure is 0.09MPa. The molar ratio of toluene to the first methanol was 5:1, and the molar ratio of toluene to the second methanol in the first reaction effluent was 4:1.
[0045] The operating conditions of the toluene tower are: tower top temperature: 115°C, tower top pressure: 170KPa, number of trays: 35, tower bottom temperature: 165°C, tower bottom pressure: 200KPa, reflux ratio: 10.
[0046] The ...
PUM
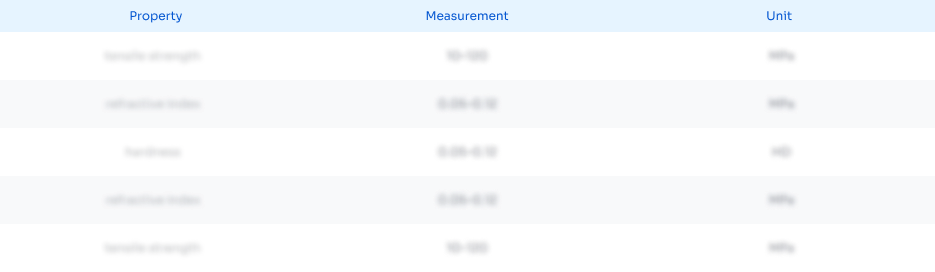
Abstract
Description
Claims
Application Information

- R&D
- Intellectual Property
- Life Sciences
- Materials
- Tech Scout
- Unparalleled Data Quality
- Higher Quality Content
- 60% Fewer Hallucinations
Browse by: Latest US Patents, China's latest patents, Technical Efficacy Thesaurus, Application Domain, Technology Topic, Popular Technical Reports.
© 2025 PatSnap. All rights reserved.Legal|Privacy policy|Modern Slavery Act Transparency Statement|Sitemap|About US| Contact US: help@patsnap.com