A whole-process process of wall forming
A whole process, wall technology, applied in the field of building materials, can solve the problems of consumption of formwork materials, smoke damage to environmental resources, poor wall integrity, firmness and shock resistance, etc. Destruction of land and environmental resources, eliminating the effect of clearing transport formwork
- Summary
- Abstract
- Description
- Claims
- Application Information
AI Technical Summary
Problems solved by technology
Method used
Image
Examples
Embodiment Construction
[0032] In order to better illustrate the present invention, it will now be further described in conjunction with the accompanying drawings. Such as Figure 1-2 As shown, in the whole process, new process and new method of new material, new structure wall brick and wall forming, the new structure wall brick adopts the hollowed out automatic centering lock seam anti-seismic wall brick (patent application number: 201310647804.6, patent application number: 201320793563.1) The embodiment structure of plane brick is as figure 1 As shown, the internal structure of the wall made of bricks is as follows figure 2 As shown in the figure, it can be seen that the interior is vertically and horizontally connected. The upper and lower bricks are inserted into each other and buckled. Finish.
[0033] Wall brick material ratio according to image 3 The range of material formulas shown in the list determines that the proportioning of the non-load-bearing wall brick materials of an embodime...
PUM
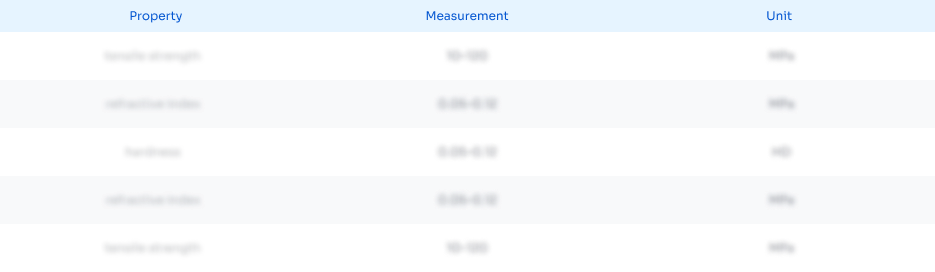
Abstract
Description
Claims
Application Information

- R&D
- Intellectual Property
- Life Sciences
- Materials
- Tech Scout
- Unparalleled Data Quality
- Higher Quality Content
- 60% Fewer Hallucinations
Browse by: Latest US Patents, China's latest patents, Technical Efficacy Thesaurus, Application Domain, Technology Topic, Popular Technical Reports.
© 2025 PatSnap. All rights reserved.Legal|Privacy policy|Modern Slavery Act Transparency Statement|Sitemap|About US| Contact US: help@patsnap.com