Printing and dyeing process for pure cotton fabric
A printing and dyeing process, pure cotton fabric technology, applied in the field of printing and dyeing of pure cotton fabrics, can solve problems such as insufficient color fastness, poor dyeing effect of pure cotton fabrics, etc., achieve visual effect improvement, wash color fastness improvement, good dyeing effect
- Summary
- Abstract
- Description
- Claims
- Application Information
AI Technical Summary
Problems solved by technology
Method used
Examples
Embodiment 1
[0015] 1) Take 2 parts by mass of hydroxypropyl methylcellulose, 2 parts by mass of dodecyltrimethylammonium sulfate, 6 parts by mass of sulfuric acid, 4 parts by mass of ammonium sulfate, 7 parts by mass of sodium sulfate, 3 parts by mass of urea, 15 parts by mass Mass parts A state pulp, 14 mass parts Acramine FWR pulp, 42 mass parts water prepare printing paste;
[0016] 2) Take 3 parts by mass of coconut oil fatty acid monoethanolamide, 7 parts by mass of silicone polyvinyl fluoride ether, 9 parts by mass of branched chain fatty alcohol condensate, 3 parts by mass of silicone, 16 parts by mass of modified 2D resin, 60 parts by mass Parts by mass of water are used to prepare the pad dyeing solution;
[0017] 3) Dyeing the bottom, dipping the fabric with the dyeing solution, the pressure is 2MPa, and the liquid carrying rate is 75%;
[0018] 4) Printing, dyeing and dyeing after adding slurry;
[0019] 5) Steaming and washing.
Embodiment 2
[0021] 1) Take 1 mass part of hydroxypropyl methylcellulose, 1 mass part of dodecyltrimethylammonium sulfate, 5 mass parts of sulfuric acid, 3 mass parts of ammonium sulfate, 6 mass parts of sodium sulfate, 2 mass parts of urea, 10 Mass parts A state pulp, 12 mass parts Acramine FWR pulp, 40 mass parts water prepare printing paste;
[0022] 2) Take 2 parts by mass of coconut oil fatty acid monoethanolamide, 6 parts by mass of silicone polyvinyl fluoride ether, 8 parts by mass of branched chain aliphatic alcohol condensate, 2 parts by mass of silicone, 15 parts by mass of modified 2D resin, 50 parts by mass Parts by mass of water are used to prepare the pad dyeing solution;
[0023] 3) Dyeing the bottom, dipping the fabric with the dyeing solution, the pressure is 1MPa, and the liquid carrying rate is 70%;
[0024] 4) Printing, dyeing and dyeing after adding slurry;
[0025] 5) Steaming and washing.
Embodiment 3
[0027] 1) Take 1.2 parts by mass of hydroxypropyl methylcellulose, 1.2 parts by mass of dodecyltrimethylammonium sulfate, 5.6 parts by mass of sulfuric acid, 3.4 parts by mass of ammonium sulfate, 6.7 parts by mass of sodium sulfate, 2.3 parts by mass of urea, 12 Mass parts A state pulp, 13 mass parts Acramine FWR pulp, 41 mass parts water prepare printing paste;
[0028] 2) Take 2.3 parts by mass of coconut oil fatty acid monoethanolamide, 6.7 parts by mass of silicone polyvinyl fluoride ether, 8.9 parts by mass of branched chain fatty alcohol ethylene condensate, 2.3 parts by mass of silicone, 15.5 parts by mass of modified 2D resin, 56 parts by mass Parts by mass of water are used to prepare the pad dyeing solution;
[0029] 3) Dyeing the bottom, dipping the fabric with the dyeing solution, the pressure is 1.2MPa, and the liquid carrying rate is 73%;
[0030] 4) Printing, dyeing and dyeing after adding slurry;
[0031] 5) Steaming and washing.
PUM
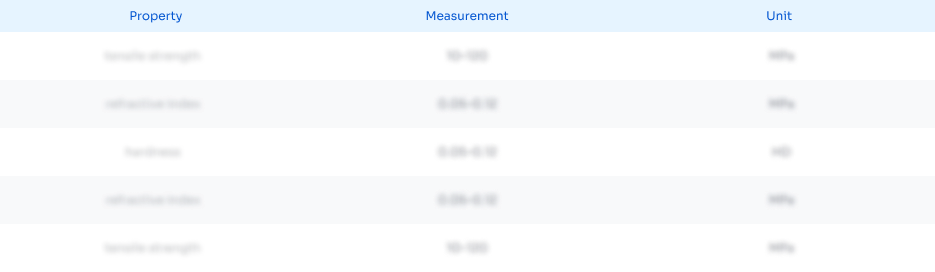
Abstract
Description
Claims
Application Information

- R&D Engineer
- R&D Manager
- IP Professional
- Industry Leading Data Capabilities
- Powerful AI technology
- Patent DNA Extraction
Browse by: Latest US Patents, China's latest patents, Technical Efficacy Thesaurus, Application Domain, Technology Topic, Popular Technical Reports.
© 2024 PatSnap. All rights reserved.Legal|Privacy policy|Modern Slavery Act Transparency Statement|Sitemap|About US| Contact US: help@patsnap.com