Process for printing and dyeing pure cotton fabric
A printing and dyeing process, pure cotton fabric technology, applied in the field of textile printing and dyeing, can solve the problems of insufficient color fastness, excessive dosage of auxiliaries, unfavorable environmental protection, etc., to achieve improved color fastness to washing, good dyeing effect, and visual effect Enhanced effect
- Summary
- Abstract
- Description
- Claims
- Application Information
AI Technical Summary
Problems solved by technology
Method used
Image
Examples
Embodiment 1
[0022] A printing and dyeing process for pure cotton fabrics, comprising the following process steps:
[0023] 1) Dyeing bottom: pad pure cotton fabric with pad dyeing solution; the raw material weight percent of described padding dyeing solution is: 3 parts of organosilicon polyvinyl fluoride ether; 4 parts of branched chain fatty alcohol-condensed cycloethylene; parts; 10 parts of modified 2D resin and 80 parts of water.
[0024] 2) Printing: Dyeing and dyeing after adding the slurry; the raw material weight percentage of the printing slurry is:
[0025] 98% sulfuric acid 10%;
[0026] Ammonium sulfate 1.5%;
[0027] Sodium sulfate 2%;
[0028] Urea 0.5%;
[0029] A state pulp 20%;
[0030] 10 parts Acramine FWR pulp 30%;
[0031] water 36%;
[0032] 3) Steaming and washing to make the coloring firm.
Embodiment 2
[0034] A printing and dyeing process for pure cotton fabrics, comprising the following process steps:
[0035] 1) Dyeing the bottom, dipping the pure cotton fabric into the pad dyeing solution; the raw materials of the padding dyeing solution are calculated in parts by weight: 5 parts of organosilicon polyvinyl fluoride ether; 1 part of silicon; 12 parts of modified 2D resin, 100 parts of water;
[0036] 2) Printing, dyeing and dyeing after adding the slurry; the raw material weight percentage of the printing slurry is:
[0037] 98% sulfuric acid 12%;
[0038] Ammonium sulfate 2%;
[0039] Sodium sulfate 3%;
[0040] Urea 1%;
[0041] A state pulp 30%;
[0042] 10 parts Acramine FWR pulp 40%;
[0043] water 12%;
[0044] 3) Steaming and washing to make the coloring firm.
Embodiment 3
[0046] A printing and dyeing process for pure cotton fabrics, comprising the following process steps:
[0047] 1) Dyeing the bottom, dipping the pure cotton fabric into the pad dyeing solution; the raw materials of the padding dyeing solution are calculated in parts by weight: 4 parts of organosilicon polyvinyl fluoride ether; 5 parts of branched chain fatty alcohol condensed cycloethylene; 0.8 parts of silicon; 11 parts of modified 2D resin, 90 parts of water;
[0048] 2) Printing, dyeing and dyeing after adding the slurry; the raw material weight percentage of the printing slurry is:
[0049] 98% sulfuric acid 11%;
[0050] Ammonium sulfate 2%;
[0051] Sodium sulfate 3%;
[0052] Urea 1%;
[0053] A state pulp 25%;
[0054] 10 parts Acramine FWR pulp 35%;
[0055] water 23%;
[0056] 3) Steaming and washing to make the coloring firm.
PUM
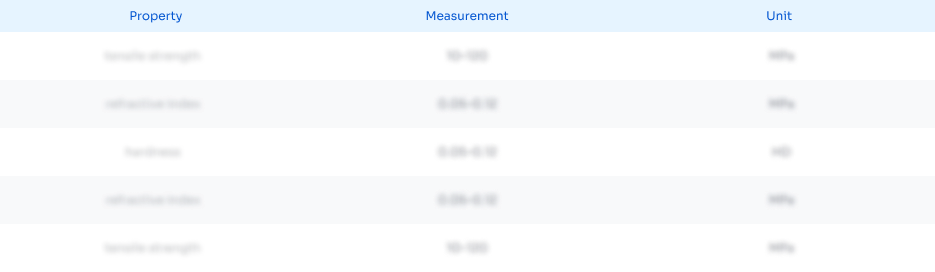
Abstract
Description
Claims
Application Information

- R&D Engineer
- R&D Manager
- IP Professional
- Industry Leading Data Capabilities
- Powerful AI technology
- Patent DNA Extraction
Browse by: Latest US Patents, China's latest patents, Technical Efficacy Thesaurus, Application Domain, Technology Topic, Popular Technical Reports.
© 2024 PatSnap. All rights reserved.Legal|Privacy policy|Modern Slavery Act Transparency Statement|Sitemap|About US| Contact US: help@patsnap.com