Preparation process of polyester fabric
A preparation process, polyester technology, applied in the field of preparation of polyester fabrics, can solve the problems of non-flame retardant, splitting, easy aging, etc., and achieve the effect of overcoming easy aging
- Summary
- Abstract
- Description
- Claims
- Application Information
AI Technical Summary
Problems solved by technology
Method used
Examples
Embodiment 1
[0013] A kind of preparation technology of polyester fabric, comprises the steps:
[0014] Preparation of polyester gray fabric, alkali weight reduction treatment, dyeing and flame retardant finishing, drying, baking, washing and drying;
[0015] Dyeing and flame retardant finishing are carried out in the same bath, the bath ratio is 2:25, the temperature is 120°C, the method of double immersion and double rolling is adopted, the excess rate is 80%, the pH of the bath solution is 6.8, and it contains the following ingredients: 35wt% phosphorus flame retardant Agent, 4g / L hexyldecanol, 40g / L disperse dye, 3g / L hydroxyethyl cellulose, 7g / L penetrant;
[0016] Coating flame retardant treatment is carried out to the cloth that has been processed by two dipping and two rolling, adopting 85 parts by mass of dimethylformamide, 130 parts by mass of polyurethane solution, 75 parts by mass of flame retardant, 12 parts by mass of closed water-based curing agent, 9 parts by mass The glue...
Embodiment 2
[0019] A kind of preparation technology of polyester fabric, comprises the steps:
[0020] Preparation of polyester gray fabric, alkali weight reduction treatment, dyeing and flame retardant finishing, drying, baking, washing and drying;
[0021] Dyeing and flame retardant finishing are carried out in the same bath, the bath ratio is 2:25, the temperature is 115°C, the two dipping and two rolling methods are adopted, the excess rate is 75%, the pH of the bath solution is 6.6, and the following ingredients are included: 30wt% phosphorus flame retardant Agent, 3g / L hexyldecanol, 35g / L disperse dye, 2g / L hydroxyethyl cellulose, 6g / L penetrant;
[0022] Coating flame-retardant treatment is carried out to the cloth that has been treated by two dipping and two rolling, adopting 80 mass parts dimethylformamide, 120 mass parts polyurethane solution, 70 mass parts flame retardant, 9 mass parts closed type water-based curing agent, 8 mass parts A rubber bag composed of an accelerator b...
Embodiment 3
[0025] A kind of preparation technology of polyester fabric, comprises the steps:
[0026] Preparation of polyester gray fabric, alkali weight reduction treatment, dyeing and flame retardant finishing, drying, baking, washing and drying;
[0027] Dyeing and flame retardant finishing are carried out in the same bath, the bath ratio is 2:25, the temperature is 118°C, the two dipping and two rolling methods are adopted, the excess rate is 77%, the pH of the bath solution is 6.7, and the following ingredients are included: 33wt% phosphorus flame retardant Agent, 3.4g / L hexyldecanol, 37g / L disperse dye, 2.3g / L hydroxyethyl cellulose, 6.7g / L penetrant;
[0028] Coating flame-retardant treatment is carried out to the cloth that has been processed by two dipping and two rolling, adopting 83 parts by mass of dimethylformamide, 125 parts by mass of polyurethane solution, 73 parts by mass of flame retardant, 11 parts by mass of closed water-based curing agent, 8.9 parts by mass The glue...
PUM
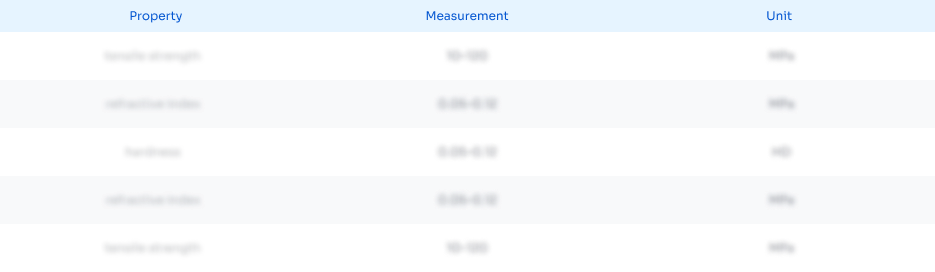
Abstract
Description
Claims
Application Information

- R&D
- Intellectual Property
- Life Sciences
- Materials
- Tech Scout
- Unparalleled Data Quality
- Higher Quality Content
- 60% Fewer Hallucinations
Browse by: Latest US Patents, China's latest patents, Technical Efficacy Thesaurus, Application Domain, Technology Topic, Popular Technical Reports.
© 2025 PatSnap. All rights reserved.Legal|Privacy policy|Modern Slavery Act Transparency Statement|Sitemap|About US| Contact US: help@patsnap.com