Acesulfame potassium cyclization continuous production method
A production method, the technology of acesulfame K, applied in the direction of organic chemistry, etc., can solve the problems of low temperature stability of the reactor, unstable cryogenic load, large production ratio error, etc., to optimize the reaction efficiency and shorten the production cycle , the effect of increasing production capacity
- Summary
- Abstract
- Description
- Claims
- Application Information
AI Technical Summary
Problems solved by technology
Method used
Image
Examples
Embodiment Construction
[0017] Such as figure 2 Shown, a kind of acesulfame cyclization continuous production method provided by the invention comprises the following steps:
[0018] 1) At the same time inject 4800kg of sulfur trioxide and 14400kg of methylene chloride into the first mixer for mixing. The reaction between dichloromethane and sulfur trioxide is negligible, and the temperature after mixing is around 24°C.
[0019] 2) Pump 6300kg of synthetic intermediates (about 1 kettle carboxylation product), specific gravity 1.24-1.26, volume 5000L, together with sulfur trioxide and dichloromethane solution from the first mixer into the second mixer, Rapid reaction in the second mixer, the temperature of the reactor is 80-110°C, the reaction time is 0.2s, the pressure is 0.6-0.9MPa, the material is sprayed from the second reactor into the sulfonation tank in the form of mist, and the injection flow rate is 0.9m / s. The sulfonation reaction is carried out at the outlet of the second mixer, the re...
PUM
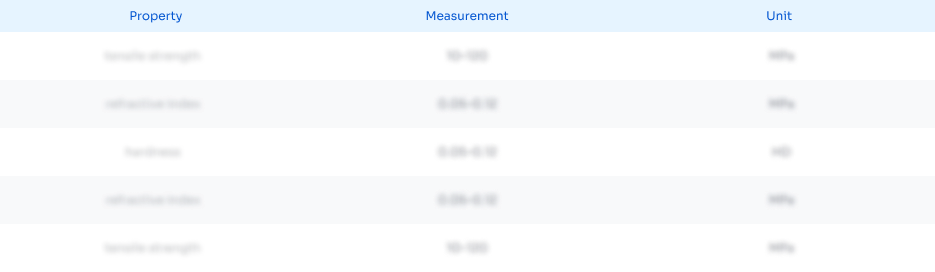
Abstract
Description
Claims
Application Information

- R&D
- Intellectual Property
- Life Sciences
- Materials
- Tech Scout
- Unparalleled Data Quality
- Higher Quality Content
- 60% Fewer Hallucinations
Browse by: Latest US Patents, China's latest patents, Technical Efficacy Thesaurus, Application Domain, Technology Topic, Popular Technical Reports.
© 2025 PatSnap. All rights reserved.Legal|Privacy policy|Modern Slavery Act Transparency Statement|Sitemap|About US| Contact US: help@patsnap.com