Two-degree-of-freedom plane translational parallel mechanism with passive hinges to be spherical hinges
A degree of freedom, spherical hinge technology, used in manipulators, program-controlled manipulators, metal processing mechanical parts, etc., can solve the problems of insufficient mechanical properties, low stiffness and dynamic performance, and achieve the effect of good stiffness
- Summary
- Abstract
- Description
- Claims
- Application Information
AI Technical Summary
Problems solved by technology
Method used
Image
Examples
Embodiment 1
[0030] combine figure 1 (a), the structure of this embodiment includes a fixed platform 1, a first set of parallel guide rails 21 and a second set of parallel guide rails 22 arranged on the fixed platform 1, and the axes of the first set of parallel guide rails 21 and the second set of parallel guide rails 22 coincide;
[0031] The first moving slider 31 arranged on the first group of parallel guide rails 21 and the second moving slider 32 arranged on the second group of parallel guide rails 22, the moving platform 7;
[0032] The first fixed-length connecting rod 51, the second fixed-length connecting rod 52, the third fixed-length connecting rod 53 connected in parallel between the first motion slider 31 and the motion platform 7, the first fixed-length connecting rod 51, the second fixed-length connecting rod The fixed-length connecting rod 52, the third fixed-length connecting rod 53 and the first moving slider 31 are respectively connected by passive ball hinges 41, 42, ...
Embodiment 2
[0041] The structure of this embodiment is as figure 2 As shown, the difference between this embodiment and Embodiment 1 is that the axes of the first group of parallel guide rails 21 and the axes of the second group of parallel guide rails 22 are arranged parallel to each other, so the first moving slider 31 and the second moving slider 32 The directions of motion are parallel to each other.
Embodiment 3
[0043] The structure of this embodiment is as image 3 As shown, the difference between this embodiment and Embodiment 1 is that the projection points of the centers of the passive ball joints 61, 62, 63 on the vertical plane where the axes of the first group of parallel guide rails 21 and the second group of parallel guide rails 22 are located are three points, The projection points of the centers of the passive spherical hinges 64, 65, 66 on the vertical plane where the axes of the first group of parallel guide rails 21 and the second group of parallel guide rails 22 are located are three points, and the first fixed-length connecting rod 51 and the second fixed-length connecting rod 52. The projection lines of the third fixed-length connecting rod 53 on the plane perpendicular to the axes of the first group of parallel guide rails 21 and the second group of parallel guide rails 22 intersect, the fourth fixed-length connecting rod 54, the fifth fixed-length connecting rod 55, ...
PUM
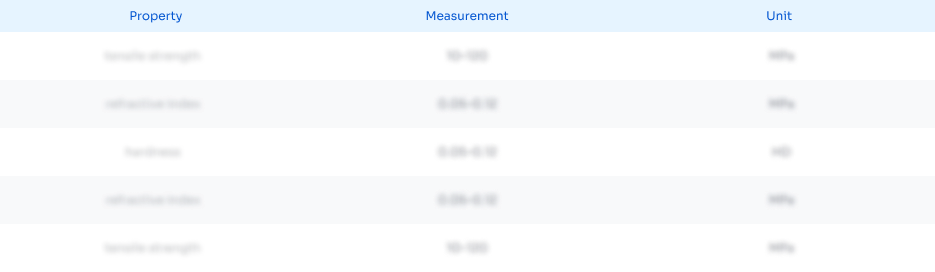
Abstract
Description
Claims
Application Information

- R&D
- Intellectual Property
- Life Sciences
- Materials
- Tech Scout
- Unparalleled Data Quality
- Higher Quality Content
- 60% Fewer Hallucinations
Browse by: Latest US Patents, China's latest patents, Technical Efficacy Thesaurus, Application Domain, Technology Topic, Popular Technical Reports.
© 2025 PatSnap. All rights reserved.Legal|Privacy policy|Modern Slavery Act Transparency Statement|Sitemap|About US| Contact US: help@patsnap.com