Radiator structure and manufacturing method thereof
A manufacturing method and radiator technology, which are applied to manufacturing tools, heat exchange equipment, lighting and heating equipment, etc., can solve the problem of long product manufacturing time, the inability of radiating fins and metal bases to be completely matched, and the long manufacturing time. And other issues
- Summary
- Abstract
- Description
- Claims
- Application Information
AI Technical Summary
Problems solved by technology
Method used
Image
Examples
Embodiment Construction
[0051] The above-mentioned purpose of the present invention and its structural and functional characteristics will be described according to the preferred embodiments of the accompanying drawings.
[0052] see figure 1 , figure 2 and image 3 , is a three-dimensional exploded schematic diagram, a three-dimensional combined schematic diagram and a schematic diagram of heat dissipation fins of the first preferred embodiment of the heat sink structure of the present invention. As shown in the figure, the heat sink 10 of the present invention includes a body 11 and a plurality of heat dissipation fins 12;
[0053] The body 11 has a first end 111 and a second end 112, a longitudinal direction a is defined between the first end 111 and the second end 112, and the body 11 has a A coupling channel 113 is distributed around the body 11 , the coupling channel 113 extends from the first end 111 along the longitudinal direction to the second end 112 and passes through the first end 111...
PUM
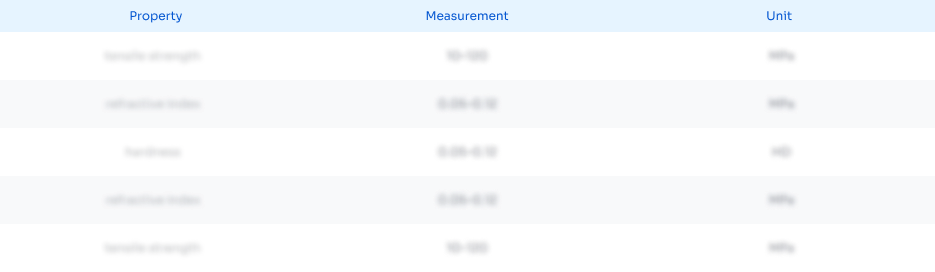
Abstract
Description
Claims
Application Information

- R&D
- Intellectual Property
- Life Sciences
- Materials
- Tech Scout
- Unparalleled Data Quality
- Higher Quality Content
- 60% Fewer Hallucinations
Browse by: Latest US Patents, China's latest patents, Technical Efficacy Thesaurus, Application Domain, Technology Topic, Popular Technical Reports.
© 2025 PatSnap. All rights reserved.Legal|Privacy policy|Modern Slavery Act Transparency Statement|Sitemap|About US| Contact US: help@patsnap.com