Extrusion moulding method for shaft parts with flanges, and special extrusion mould
A technology for extrusion forming and shaft parts, which is applied in the direction of metal extrusion dies, etc., can solve the problems of inability to form rod shaft parts, high equipment investment cost, and large tonnage of forming equipment, so as to achieve small extrusion force and reduce The effect of small input and extrusion area
- Summary
- Abstract
- Description
- Claims
- Application Information
AI Technical Summary
Problems solved by technology
Method used
Image
Examples
Embodiment Construction
[0026] An embodiment of the extrusion forming method of a shaft part with a flange of the present invention: as Figure 1 ~ Figure 3 As shown, the extrusion molding method includes the following steps, 1) will be as figure 1 The extrusion molding die shown is installed on a double-acting hydraulic press, and the double-acting hydraulic press has two power output shafts, the outer cylinder located on the inner side and the inner cylinder located on the outer side. Figure 4 The blank with diameter D1 and height h shown is put into figure 1 In the die 9 of the extrusion molding die shown, the extrusion molding die comprises a first outer punch 8-1, the first outer punch 8-1 is provided with a central hole extending along its axial direction, and the first outer punch A step surface is arranged on the outer peripheral surface of the mold, and the step surface is set toward the side of the die. A first inner punch 6-1 is installed inside the first outer punch 8-1, and the first i...
PUM
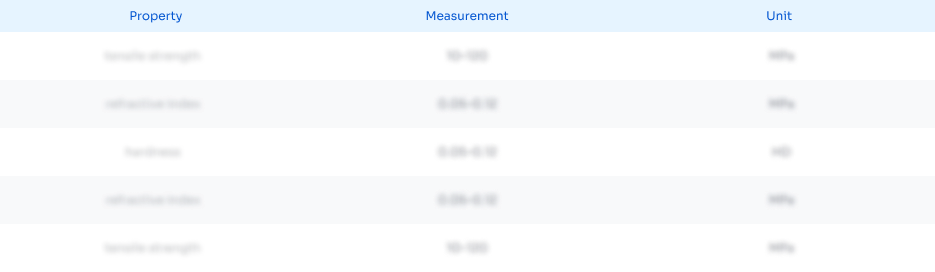
Abstract
Description
Claims
Application Information

- R&D
- Intellectual Property
- Life Sciences
- Materials
- Tech Scout
- Unparalleled Data Quality
- Higher Quality Content
- 60% Fewer Hallucinations
Browse by: Latest US Patents, China's latest patents, Technical Efficacy Thesaurus, Application Domain, Technology Topic, Popular Technical Reports.
© 2025 PatSnap. All rights reserved.Legal|Privacy policy|Modern Slavery Act Transparency Statement|Sitemap|About US| Contact US: help@patsnap.com